Compression molding is a popular manufacturing process that involves placing a preheated material in a mold cavity and applying pressure until it takes the shape of the mold. Producing various products, including automotive components, electrical enclosures, and consumer goods, is cost-effective.
However, it’s crucial to consider several factors when designing for compression molding to achieve the desired outcome. In this article, we’ll discuss these factors in material selection.
The first factor to consider when designing for compression molding is material selection. Different materials have varying properties that affect the final product’s quality and performance.
For instance, the material’s flow rate and viscosity can affect how easily it fills the mold cavity, while its thermal conductivity can influence the heating and cooling rates. Some materials can shrink or expand during the process, affecting the final product’s dimensional accuracy.
Selecting a material compatible with the process is crucial and can produce the desired results.
Part geometry and complexity
The complexity of the part geometry is another critical factor to consider when designing compression molding. Parts with complex shapes or features may require multiple steps or stages in the molding process, which can increase the manufacturing time and cost.
Moreover, complex shapes can affect the material flow and distribution, leading to voids or defects in the final product. To overcome these challenges, designers must consider the part’s geometry and design it to ensure proper material flow and distribution.
Draft angles and undercuts
Draft angles and undercuts are also essential factors to consider when designing for compression molding. Draft angles are necessary to ensure the part can be quickly ejected from the mold without causing damage.
The angle should be sufficient to allow the part to release smoothly without interfering with the mold’s texture or details. Conversely, undercuts can make removing the part from the mold cavity difficult. Designers must incorporate appropriate draft angles and minimize undercuts to ensure easy and smooth ejection of the part.
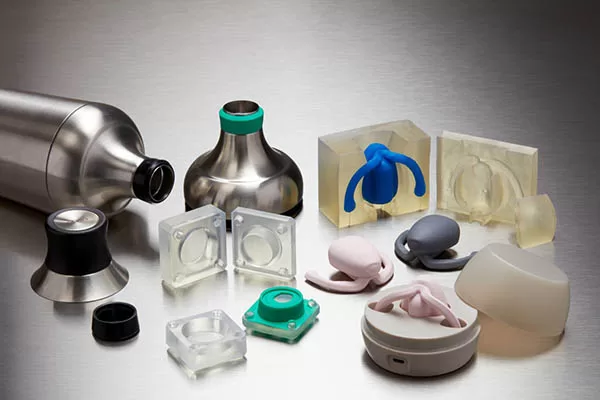
Compression molding products
Wall thickness and rib design
Wall thickness and rib design are also crucial factors to consider when designing for compression molding. Thin walls can lead to warping or distortion of the part during cooling, while thick walls can cause sink marks or voids.
Designers must consider the material’s flow characteristics and the part’s structural requirements when determining the wall thickness. Similarly, rib design can affect the part’s strength and stiffness. Designing the ribs to ensure even material flow and minimize the risk of sink marks or voids is crucial.
Tooling and mold design
Finally, tooling and mold design play a critical role in the success of compression molding. The mold design should be such that it allows for proper material flow and minimizes the risk of defects.
Similarly, the tooling must be designed to withstand high pressure and temperature during the process. The mold and tooling design should be such that they can be easily maintained and repaired, minimizing downtime and maintenance costs.
Conclusion
In conclusion, designing for compression molding requires careful consideration of various factors. Material selection, part geometry, draft angles, wall thickness, rib design, and tooling/mold design are critical factors that must be considered to achieve high-quality, cost-effective production runs. By considering these factors, designers can optimize the compression molding process and produce products that meet the desired specifications.