There are two broad, rapid tooling categories. One involves approaches indirectly making use of quick tooling master techniques for producing a mold. The other uses an approach directly where the machine of rapid tooling creates the real core and cavity mold insert.
The demand for quicker and less costly tooling solutions resulted in a majestic number of rapid tooling techniques developed globally. Many organizations are following rapid tooling development as well as commercialization because of the market prospect. Each process includes many strengths that are countered by a few limitations. This creates solutions that can cater to some niche applications. Still, due to their possible impacts, such developments are leading to many inquiries from several organizations. Innumerable manufacturing organizations are also working very hard to determine if it is the right time for phasing in on such approaches.
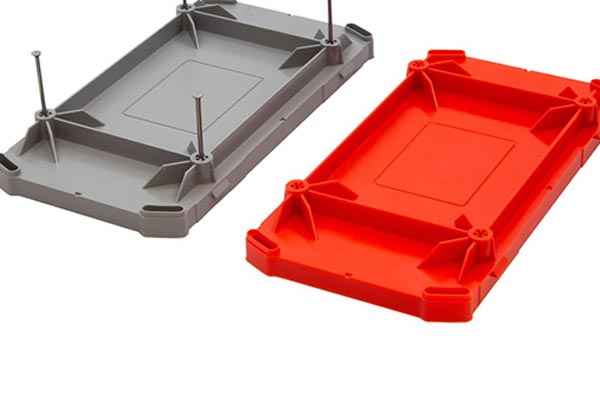
Vacuum casting products
Indirect rapid tooling methods
Many pattern-based procedures are developed to create a mold fast with different costs, lead time, and procedure capabilities. The exactness of such processes hangs on the used rapid tooling procedures’ accuracy for creating the patterns. Some indirect quick tooling methods are:
Vacuum Casting: Some plastic parts can be vacuum cast by putting one silicone tool in any vacuum chamber by using polyurethane resin. It is mixed and then de-gassed before pouring into the silicone cavity. Later the vacuum gets released, and then the tool gets removed to any post-curing oven toll 2 hours based on the size of the device. Then the cavity will be opened, and the polyurethane part will be removed. Then the pit is closed, and the entire procedure is repeated.
Wax injection molding: The silicone cavity is also appropriate for investment casting where waxes are injection molded at low pressure. Please make use of low pressure and injection system, semi-molten wax will be forced within the cavity till it becomes full. Then it is chilled before the wax becomes completely solidified. Then it is entirely removed from the silicone cavity, and the total procedure is repeated. Too much care needs to be provided when you remove wax parts from it due to the weakness of casting wax materials.
Sprayed Steel: Here, the atomized material gets deposited by making use of on spray gun. Many spray heads get involved. This procedure will produce tough tools, and this is a very functional procedure than conventional sprayed steel tooling. The main benefit of this procedure is that this will work great for large tools mostly as steel metal stamping goes away. It will offer a high deposition rate and will be less costly compared to traditionally machined metal tooling. The tool cost, fees of license, and limitations related to spraying into the slots and holes are big disadvantages.
Final words:
So, there are different types of rapid tooling techniques. Most will need an excellent pattern, but an expanding number offers a path directly for making up the tooling. Indirect procedures of rapid tooling will keep on flourishing as these ones are highly developed.