Tools or more commonly known as dies are needed in every manufacturing process. It has become significant that the annual turnout for the tooling industry is close to 60 billion dollars. In the past, the tool-making industry was dominated by Western economies like the US, Japan, and the UK. These days, there are a lot more countries involved,
The technological advances and increasing automation, namely the use of CNC machines have led to producing simpler tools for commodity products. Whenever a new design is developed, the tooling process usually takes longer. This delay can affect the overall production process. Aside from that the tools also form a significant part of the financial investment.
The good news is manufacturers can now have access to rapid tooling, a faster and cost-effective way of creating tools for presentation and product evaluation. It can also be used for bridge production before a particular part will go for full production.
Direct and Indirect Rapid Tooling
There are many attempts made to develop a new manufacturing technique that would cut the production time for tooling. It has become a quest for many industries, and there are different solutions available.
The first approach is classified as direct tooling, where the tool is manufactured from a CAD. It’s called CNC machining where the machine takes away a piece of the block to form the part.
Another tooling process is where the machine builds a 3D shape from nothing through the additive method. This approach is indirect tooling where the tool is formed using an intermediate step known as the “master”. This is the master model which is a 3D representation and where the subsequent copies will be made many times over to create the tool.
The latter may be retrogressive because introducing another step is counterproductive when direct tooling can be used even without it. However, indirect tooling is a necessary step to make sure that the production of tools that are required to be robust and strong is needed to produce a high volume of parts or products. This is critical to ensure that it’s error-free.
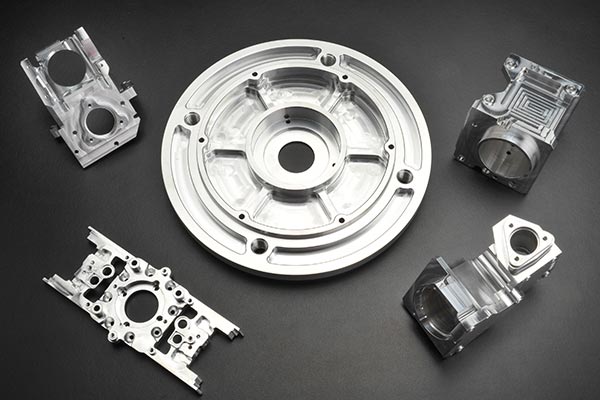
Rapid prototyping products
Advantages and Disadvantages of Rapid Tooling
Direct tooling can offer faster lead times. Instead of waiting for months, this rapid tooling process can make tools in a matter of weeks, especially with low volume requirements. Some of the examples where direct tooling is used include layered object manufacturing for laser-cut steel sheets, laser sintering of a powder bed, and 3D welding. In laser sintering, the powdered steel is fused to create a particular shape using a laser beam.
The major disadvantages of direct tooling are the restricted size capacity and limitation on the robustness of the tools. The tools produced through direct tooling are only effective for short runs around 5,000 and not beyond.
For the indirect tooling process, where the “master” is a requirement, the master pattern is usually left unscathed by the process. It can be re-used and there is only a single cost of producing the tool. However, indirect tooling is only applicable to soft tooling in short-run productions and hard tooling for high-volume productions.