Pressure die casting is a manufacturing process that allows for the mass production of high-quality metal components. This technique is particularly advantageous for consumer durables, enabling precision and consistency in creating complex shapes. This method can achieve lightweight yet durable products that meet the demands of modern consumers.
The pressure die casting process involves forcing molten metal into a mold under high pressure, which ensures intricate details and a smooth finish. This capability is essential for consumer durable goods, where aesthetic appeal and functionality are paramount. With this approach, manufacturers can deliver products that perform well and attract consumers through their design.
Understanding the benefits of pressure die casting can help you make informed decisions about product development and material choice. As markets evolve, embracing advanced manufacturing techniques like this can set your products apart in a competitive landscape.
Overview of Pressure Die Casting
Pressure die casting is a highly efficient manufacturing process that involves injecting molten metal into a mold under pressure. This technique is particularly effective for producing intricate shapes with high precision and minimal waste. Key aspects include the fundamentals of the die casting process, its advantages, and the materials typically used.
Fundamentals of the Die Casting Process
The pressure die casting process starts with creating a mold, usually made from steel or iron, to withstand high temperatures and pressure. Molten metal is injected into the mold using a piston mechanism, which enables the metal to fill intricate cavities quickly.
Cooling and solidification occur rapidly, resulting in a finely detailed part. After solidification, the mold is opened to release the finished component. This process is suitable for high-volume manufacturing, ensuring consistency and scalability in production.
Advantages of Pressure Die Casting in Manufacturing
Pressure die casting offers numerous advantages, making it a preferred choice for consumer durable products. One significant benefit is the ability to produce parts with complex geometries. This flexibility allows for innovative designs that enhance product functionality.
Speed is another significant advantage. The quick cycle times enable mass production, reducing per-unit costs. Additionally, the process generates minimal scrap compared to other methods like machining, improving material efficiency.
The dense microstructure of die-cast components enhances durability. This results in strong, lightweight products that meet rigorous performance standards, which is crucial for consumer durables.
Materials Commonly Used in Pressure Die Casting
Several materials are commonly utilized in pressure die casting. Aluminum is the most popular due to its lightweight properties and excellent corrosion resistance. It is often used in automotive and electronics applications.
Zinc is another frequently used material. It provides good fluidity and detail reproduction, making it ideal for intricate designs.
Magnesium offers a high strength-to-weight ratio, which is applicable to aerospace and sporting goods. Each of these materials has specific properties that suit various applications in consumer durable products.
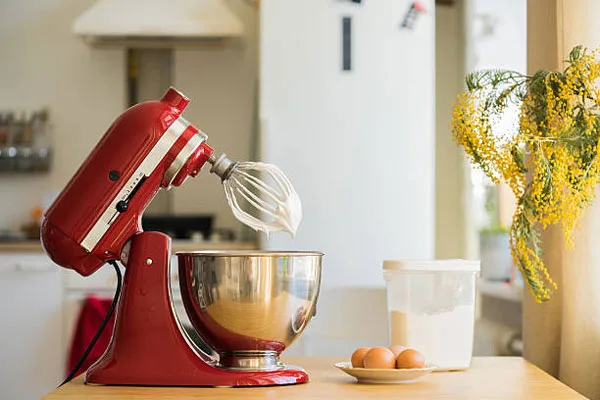
mixers
Pressure Die Casting Application in Consumer Durables
Pressure die casting plays a crucial role in manufacturing various consumer durable goods. This process allows for precision and efficiency, ensuring high-quality and cost-effective products.
Consumer Electronics and Household Appliances
In consumer electronics, pressure die casting is essential for producing components such as housings and structural parts. These parts require tight tolerances and lightweight characteristics, which die casting can effectively achieve.
This method also benefits household appliances like mixers, blenders, and toasters. Aluminum alloys are popular due to their thermal conductivity and resistance to corrosion. Manufacturers can create intricate designs that enhance functionality and aesthetics by using pressure die casting.
Automotive Components for Consumer Use
Pressure die casting is heavily utilized in producing automotive components for consumer use. This method commonly manufactures parts such as engine blocks, transmission cases, and brackets.
The strength-to-weight ratio achieved by using die-cast aluminum or zinc means fuel efficiency and performance enhancements. Additionally, creating complex geometries allows for integrating multiple functions within a single part, streamlining assembly for automotive producers.
Quality Control and Testing of Cast Products
Quality control is critical in pressure die casting, as any defects can lead to significant failures. Rigorous testing methods, such as X-ray inspection and mechanical testing, ensure that components meet industry standards.
You should expect procedures that include examining surface integrity and dimensional accuracy. Non-destructive testing methods allow manufacturers to identify potential issues without damaging the finished products. This emphasis on quality results in a reliable end product suitable for demanding consumer markets.
For your manufacturing needs, consider reaching out to Nicerapid.com. Their expertise in pressure die casting will help you achieve high-quality results tailored to your specific requirements.