Do you want rapid prototype development? Do you need a fast transition into mass production? Multi-cavity injection molding is a great choice for plastic and silicon components.
What is a multi-cavity mold? How does it differ from other types of injection mold tooling? Is it the ideal choice for your production requirements and budget?
We’ll look at the answers to all these questions and more in this post.
What Is a Multi-Cavity Injection Mold?
A multi-cavity mold is a tool used in the prototyping and mass production of components for various industries.
The technology offers rapid production of precision parts, with high-quality standards and easy replication of advanced components.
These molds can contain anywhere from two to 128 parts or more, depending on manufacturing requirements.
Single-Cavity vs. Multi-Cavity Molding
Single-cavity molds are a good choice for fast, low-cost prototyping projects. You get quick delivery time on the mold, shorting projects, and getting faster to market.
However, you don’t get the same part-per-cycle production capability that you do with multi-cavity molds.
Multi-cavity molds can cope with producing several different components in a single mold or replicating the same part.
What are the Pros & Cons of Multi-Cavity Injection Molding?
Multi-cavity mold tooling offers manufacturers a solution for both rapid prototyping and production. Here are some pros and cons of this technology.
Multi-Cavity Mold Pros
- Higher part-per-cycle rate for bigger production volumes.
- Lower cost-per-part than single-cavity molds.
- Ideal for creating color consistency in parts.
- Create a set of parts in a single mold for faster production times.
Multi-Cavity Mold Cons
- The lead time for making a multi-cavity mold is much longer than a single-cavity tool.
- Multi-cavity molds are more expensive to manufacture and finish.
- These molds require extensive QC checks to ensure the predictability and repeatability of the mold under high-stress ss-production environments.
- Multi-cavity tools require more gate & runner systems and cooling channels.
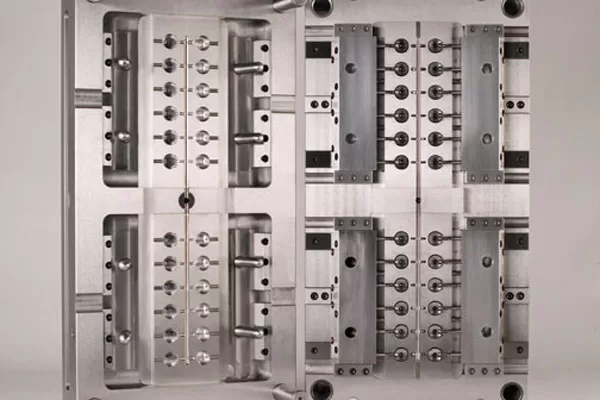
Multi cavity mold tool
Understanding How Multi-Cavity Molds Affect Production Cycle Times
The production cycle time offered by the mold is essential for mass production purposes. However, the mold must produce consistent product quality. The product cycle time impacts the number of parts made in a specific period, allowing for complete predictability and control in manufacturing processes.
So, the production time essentially governs the company’s output and the time it takes to get high-demand products into consumers’ hands. When order volumes rise, manufacturers will reduce cycle times to as few as possible.
For manufacturers to reach the fastest delivery time per cycle, they may require an additional investment in tooling quality. The need for specialist metals to endure high-volume production levels can be markedly different from single-cavity molds.
However, over the long run, when used correctly, a multi-cavity mold can accelerate production times, reduce costs, and minimize logistical problems.
In Closing – Consideration Factors for Multi-Cavity Projects
So, which mold type suits your next production project? Before committing your investment capital to a specific tooling idea, here are some factors to consider.
Project Complexity
Complex prototype manufacturing increases project costs. The mold costs more, and the more intricate the design. You can expect longer lead times and higher design costs with more complicated projects.
Tooling Capabilities
What kind of volume are you looking for in your product manufacturing requirements. Do you need 12, 128, or 1,000 items per mold?
Tooling Cost
The materials used in the mold itself, such as stainless steel or aluminum, increase or decrease depending on your project requirements. The number of cavities required, and the intricacy of each cavity design play a role in the price of the mold, as does its finishing.
Materials
What kind of products do you want to create? Can you benefit from LSR or plastic injection molding production strategies?