Silicone is a versatile material commonly used in rapid prototyping projects for many industries. This material is cost-effective, highly durable, and has precise components with many different finishes available.
LSR, or “liquid silicone rubber,” is commonly used in injection molding processes. It creates parts and components with consistent and reliable mechanical and physical properties. The process can produce components in various sizes, in high volume, at lower cost, making it an ideal material for rapid prototyping and mass manufacturing projects.
LSR is available in various “shore hardness” or durometer grades, describing the properties of the rubber and its firmness. For instance, 50 shore is softer than 60 shore silicone. The range of hardness allows for the production of many different parts for various industries, from automotive to aerospace.
The consistency in the curing process means that silicone materials are ideal for producing parts used in the medical industry, allowing for repeatable quality with every batch. This post examines the different types of materials used in silicone molding.
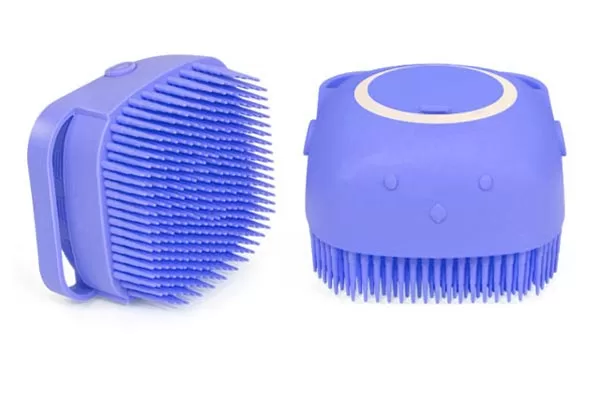
Pet cleaning brushes
Types of Silicone Suitable for Molding
Room Temperature Vulcanizing (RTV) Silicone
This dual-component material cures readily at room temperature and is easy to handle and use. RTV is most commonly used in rapid prototyping processes because it is suitable for smaller production runs and one-off designs, has a shorter curing time, and is less durable than other options.
High-Temperature Vulcanizing (HTV) Silicone
This dual-component material requires the application of heat to cure. This silicone compound can withstand higher operating temperatures than RTV, making it ideal for creating heat-sensitive components.
Materials Used in Silicone Molding
Selecting the right type of silicone for your project depends on the specific requirements of the components. You’ll need to consider factors like mechanical properties, the curing process, and hardness range.
Successful prototyping projects and mass production ventures largely rely on choosing the right materials for the task. Here are the most common silicone materials used in molding applications.
Silicone Rubber
This highly versatile material has widespread industry use due to its excellent mechanical properties. Here are the top features of silicone rubber relating to its use in silicone molding applications.
- Excellent elasticity and high tear strength.
- Good chemical and temperature resistance.
- Excellent insulative properties.
- Low compression set.
Silicone rubber is available in a wide range of shore hardness ranging from super soft Shore A10 to super hard Shore A90. It’s suitable for rapid prototyping projects but might not be the best choice for mass production of precision parts, such as those for the medical and aerospace industries.
Liquid Silicone Rubber (LSR)
LSR is the most common silicone material used in high and low-volume production. This thermosetting polymer is a high-quality form of silicone with great mechanical properties and consistent curing for accuracy in the final parts produced. It has excellent curing times and is the better choice for making components demanding high degrees of accuracy and precision.
Some of the advantages of using LSI in your rapid prototyping and mass production projects include the following.
- Fast curing times.
- A high degree of consistency in manufactured components.
- Excellent mechanical properties make it highly durable and functional.
- Less waste and lower costs.
Like silicone rubber, LSR is available in a range of shore hardness, from Shore A10 to Shore A90.
Other Common Materials in Silicon Molding
The silicone molding process may require the manufacturer to add other components to the silicone rubber or LSI to alter its properties according to the part’s final specifications.
Colorants can change the color of the silicon from off-white to any color imaginable. Manufacturers may add fillers to alter the mechanical properties of the LSI or silicone rubber. Adhesives help to bond the silicone rubber or LSI to other materials.
Implementing Silicone Molds
Silicone molds are a key component in liquid silicone rubber (LSR) injection molding processes. They also play a big role in the quality of finished parts. Silicone molds are advantageous for rapid prototyping and mass-production projects due to the flexibility of adapting to low and high-volume production requirements.
Precision tooling allows manufacturers to produce consistent parts in complex shapes with minimal need for post-production processing. Silicone molding produces consistent parts and is suitable for manufacturing intricate designs with tight tolerances.
A manufacturer creates the silicone mold by injecting a thermosetting polymer into a cavity. The manufacturer cures the mold, and the finalized form is now ready for use in producing LSR products. The curing process has seen a reduction in curing times thanks to recent technological advancements. The results are shorter cycle times and the capability for faster results in mass production environments.
When using silicone molds, manufacturers must ensure the materials are compatible with LSR processes to ensure optimal performance and no waste. Using the right materials means you can expect consistency in each part’s mechanical properties and shape.
The material used in the molding process must withstand the forces involved in the mixing process, or it loses its thermal stability and produces poor results. This results in more waste and increased project expenses, with no beneficial outcome.
The use of silicone mold manufacturing practices enables the aerospace and medical industry to receive highly accurate results for finished parts. There’s less risk of failure, and it allows for the production of affordable parts at scale.
As a result, the use of silicone molding is highly popular in rapid prototyping and mass production due to its flexibility and ability to produce components at high or low volumes. That’s why it’s so common across all industries for use in a range of projects.
In Closing
Silicone molding is a common production method used in low- and high-volume applications. Silicone allows for the consistent production of highly accurate and precise parts. Several different grades of silicone materials are available for molding projects, each of which has unique properties for various applications.
Designers and manufacturers must consider the correct material option for the project before committing resources to it. It’s essential to have the guidance of an experienced manufacturing partner when planning your project. The right team can help you achieve your goals.