Makeup is a billion-dollar industry, with companies investing millions in product research and development. Silicone molding offers an attractive manufacturing process for mass-producing products at scale for global distribution.
Manufacturers can assist brands with creating silicone products with features manufactured using the latest injection molding techniques. Brands benefit from speedy project development, prototyping, and optimal production.
Silicone Molded Makeup Products
There are dozens of examples of silicon-molded makeup products. Some of the more common items you might already use in your daily beauty routine include the following cosmetics products.
- Mascara brushes
- Makeup packaging
- Lipstick casings
- Makeup applicators
The Silicone Injection Molding Process for Makeup Products
The manufacturer selects the right grade and type of Liquid Silicone Rubber (LSR) that suits the product’s specific functions and features to meet the consumer’s application. LSR’s differentiating characteristic is its biocompatibility, excellent compression set, and chemical and temperature resistance up to 500F.
- LSR is chemically inert, making it hypoallergenic, biocompatible, and non-allergenic. It’s the ideal manufacturing material and method for various makeup products, baby items, food products, and medical instruments.
- LSR is reliable compared to TPE and rubber when resolving ingredient interaction or migration problems. The chemical stability of LSR makes it ideal for contact with water, skin, blood, etc.).
- LSR molded products utilize a manufacturing process involving cross-linking agents and a catalyst, pumped into drums before blending in a static mixer. Additives and color pigments can be added according to customer requirements.
Gravity forces the material to flow into the injection screw, where its transported to the mold, with the material remaining at room temperature. The manufacturer then injects the LSR into the mold, heating it between 170°C and 200°C to vulcanize the material and create its final form.
- When raw materials are pre-mixed, the blend is constant between batches.
- An automated manufacturing process guarantees production consistency and quality, giving repeatable results.
- Multi-cavity molds offer huge increases in productivity with short cycle times.
- Direct injection eliminates waste.
- No post-production deburring.
- Reduced labor requirements due to automated handling systems.
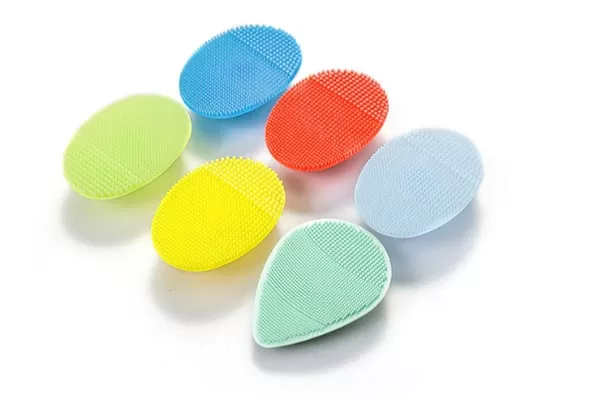
Skin care make-up spin massage silicone brushes
The Advantages of Using Silicone Molding for Makeup Products
LSR is the ideal material for makeup products. It’s flame retardant and suits industry requirements for safe manufacturing. Experts believe that LSR will replace the use of traditional PC in a range of applications, including makeup products.
There are several advantages to using LSR molding technology in makeup product manufacturing.
The Advantages of LSR in Makeup Product Quality
- Excellent hot and cold temperature resistance ranging from -45°F up to 500°F)
- Excellent compression set.
- Stable, pure, inert, adaptable, and durable,
- Taste and odor neutral.
- Excellent adhesion qualities
- Weathering and age resistance
- Biocompatible.
The Advantages of LSR in Makeup Product Finish
- Soft-touch surfaces.
- Crystalline and transparent.
- It can be mixed with additives.
- Many colors are available.
- Materials available in 1 shore A (soft) up to 90 shore A (hard)
The Advantages of LSR in Makeup Product Safety
- Antimicrobial and hypoallergenic.
- Easy to sterilize with steam, gamma radiation, and ethylene oxide.
- Meets requirements for approval on standards like FDA 21 CFR 177.2600, BfR XV, and USP Class VI.
Silicone injection molding offers makeup brands and manufacturers several key advantages for optimizing their product development and production.
- Fast production – Manufacturers can produce several molds in a matter of months and move from prototyping to mass production in a matter of months.
- Low labor costs – Highly automated processes remove labor costs and drive down manufacturing expenses.
- Different Solidity – Products can feature different rigidity or flexibility according to application requirements.
- Complex Design – Mass production of identical units with complex components.
- Eco-friendly Production – Minimal waste.
Makeup brands rely on LSR manufacturing processes to ensure they remain on the cutting edge of a competitive market. With fast prototyping and production, LSR molding offers makeup brands a faster time-to-market when introducing new products.