Silicone molding creates flexible, durable components using specialized silicone rubber materials. This process produces parts that maintain performance across extreme temperature ranges and harsh environmental conditions.
The Silicone Molding Process Breakdown
Silicone molding begins with mixing liquid silicone rubber compounds. These materials cure through chemical reactions, rather than simply cooling, like thermoplastics.
Injection systems deliver the mixed silicone into heated molds. The heat accelerates the curing process, creating cross-linked polymer chains.
Curing times vary based on part thickness and silicone formulation. Most parts cure completely within 30 seconds to 5 minutes.
Demolding occurs after full cure completion. The flexible nature of silicone allows removal from complex geometries without damage.
Key Advantages of Silicone Molding Technology
Temperature resistance spans from -65°F to 400°F for most silicone grades. Some specialty formulations handle even more extreme conditions.
Chemical compatibility makes silicone suitable for medical and food contact applications. The material is resistant to most solvents and cleaning agents.
Flexibility retention occurs throughout the material’s service life. Repeated flexing and compression do not cause permanent deformation.
Biocompatibility meets strict medical device regulations. USP Class VI and FDA-approved grades ensure patient safety.
Applications Driving Silicone Molding Demand
Medical devices represent the largest market for silicone molding. Gaskets, seals, catheters, and implantable components all use this technology.
Automotive applications include engine gaskets, weatherstripping, and vibration dampeners. The temperature and chemical resistance prove essential for vehicle performance.
Consumer electronics benefit from silicone’s electrical insulation properties. Phone cases, keyboard buttons, and cable insulation use molded silicone components.
Industrial equipment relies on silicone seals and gaskets. The material’s performance in extreme conditions prevents costly equipment failures.
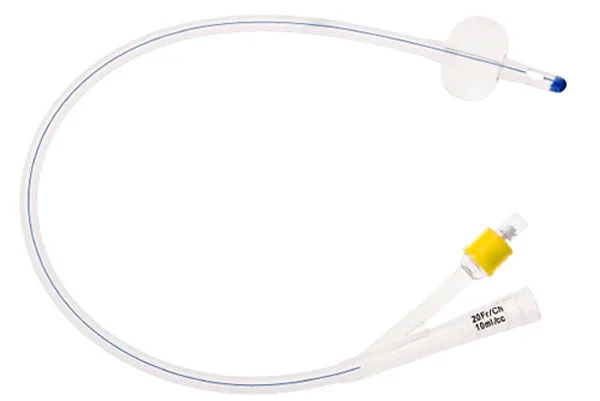
Silicone urinary catheter
Material Grades and Selection Criteria
General-purpose silicones handle most standard applications. These materials strike a balance between cost and performance for typical operating conditions.
High-temperature grades withstand continuous exposure above 400°F. Aerospace and industrial applications often require these specialty materials.
Medical-grade silicones meet strict purity and biocompatibility standards. Implantable and skin-contact applications mandate these certified materials.
Conductive silicones incorporate carbon or metal fillers. Electronic applications utilize these materials for electromagnetic shielding and grounding purposes.
Design Optimization for Silicone Molding
Wall thickness affects cure time and part quality. Thicker sections require longer cure cycles and may develop internal voids.
Draft angles facilitate part removal without tearing. Silicone’s flexibility allows smaller draft angles than rigid plastic materials.
Undercuts become possible due to silicone’s ability to stretch. Complex geometries that challenge other molding processes work well with silicone.
Surface texture transfers directly from the mold surface. Smooth, textured, or patterned finishes achieve excellent reproduction quality.
Production Considerations for Success
Cycle times depend on part geometry and silicone formulation. Thin-walled parts cure faster than thick sections.
Mold maintenance requires special attention to cure residue buildup. Regular cleaning maintains surface quality and dimensional accuracy.
Quality testing focuses on physical properties and dimensional verification. Tear strength, compression set, and hardness measurements ensure compliance with specifications.
Secondary operations include trimming, printing, and assembly. Many silicone parts require finishing operations before they are used in their final form.
Transform your flexible component requirements into reality with professional silicone molding services. Contact Nice Rapid today to discuss your project specifications and learn how our specialized outsourcing services deliver precision-molded silicone components that meet your exact performance requirements.