Designing and producing face masks is a technically challenging process. However, it is an established process. There are many types of masks, from the respiratory breathing masks in the hospital to the C-PAP masks people use to stop sleep apnea and the face masks we wore during the pandemic.
This post examines mask production using liquid silicone rubber (LSR). LSR is a common material used in rapid prototyping and mass production processes. It’s also a frequently used material in mask design.
Hospitals and emergency services have used silicon masks for a long time, and they’re also commonly used in at-home oxygen treatments and in sleep apnea therapy. The mechanical properties of LSR make it an ideal material for mask production. Many masks consist of several materials molded into the same model, and there are several production methods for making them.
For example, the mask housing might feature construction with thermoplastics and the nose and mouthpiece from LSR. Mask design may also allow for the insertion of filter systems. Established mask manufacturers rely on single and multi-component injection molding processes to manufacture medical-grade masks.
Since most masks are utilized in medical treatments and procedures, manufacturers must produce masks using FDA-approved materials. LSR offers an FDA-approved material suitable for manufacturing masks used in the industry. LSR offers excellent mechanical properties and a high degree of reliability in rapid prototyping and mass production processes.
The hypoallergenic, biocompatible, and neutral odor and taste of LSR give it excellent all-round properties. It’s a heat-resistant material and allows for design flexibility and combination with other manufacturing materials.
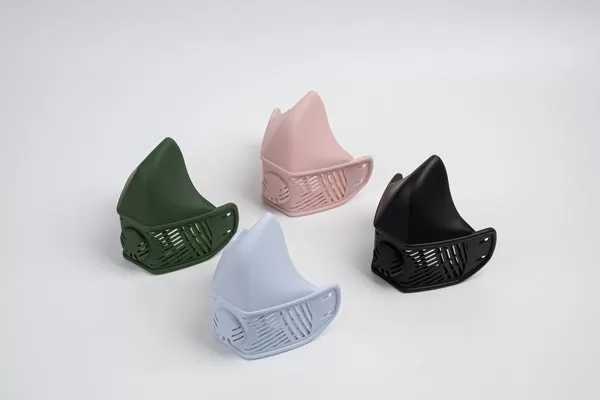
Silicone masks
LSR & Multi-Material Injection Molding Technology
LSR is processed using multi-component or 2K technology. This method allows for several combinations of LSR in different shore hardness to be used in a single mask design. It’s also possible to combine LSR with thermoplastics.
Some mask designs feature design and construction with advanced engineering plastics such as PPS, PEEK, PSU, PA, PBT, PMMA, PC, and PET, which make great additions to LSR materials in mask production, and it’s also possible to bond metals, fiberglass, and glass into the LSR.
Some of the other benefits of using LSR are its low compression set, excellent resilience, and high tear resistance. It’s also possible to dye it any color.
From functional designs requiring thick silicone to thin face coverings, the requirements of mask production are many. Introducing new designs to mask production presents several challenges for manufacturers.
The requirements for material processing and mold making are extensive, and it’s important for manufacturers to take ergonomics into consideration when designing and planning new face mask products.
Silicone-only masks (1K) feature design with varying silicone thicknesses in different locations around the mask. The thickness may be greater in functional regions of the mask while thinner in some areas.
There may also be requirements for different textures around areas of the mask, adding complexity to the manufacturing process. Low-viscosity LSR materials are especially challenging to work with in terms of mold design, manufacturing, and production.
When working with these materials, it’s critical for manufacturers to pay attention to process stability and repeatability, ensuring consistent quality in all products rolling off the production line.
The Advantages of LSR in Mask Production
The development time for silicone masks is extensive compared to the typical N95 and surgical face masks we’re all used to after the pandemic. However, there are very different design principles, materials, and manufacturing differences between these face masks and LSR masks.
The design and development stages are extensive, and the rapid prototyping phase may involve several designs before settling on the final product for mass production. Silicone offers manufacturers an easy material to work with, with a high degree of sustainability.
- Here are the top benefits of LSR in mask design and production.
- Hypoallergenic, biocompatible, and neutral in taste and odor.
- Resistant to water, solvents, alcohol, and weaker acids.
- Excellent temperature resistance properties for high and low temperatures.
- The 5-shore LSR material is comfortable and soft on the face, making it easy to wear.
- Ideal for use in 2K injection molding manufacturing processes.
- Allows for the insertion of other materials, such as thermoplastics.
- Excellent design flexibility.
Final Thoughts – Challenges in LSR Mask Production
It’s challenging for manufacturing partners to plan mask prototyping and production processes. For instance, the 3D free-formed mask elements make calculating the materials flow front difficult.
While it’s possible to simulate the design and molding, it’s essential to have qualified and experienced application engineers to overcome the hurdles involved with the prototyping of mask products and their mass manufacture.
If the manufacturer uses fully automated manufacturing processes for mask production, they need space for handling during the demolding process and positioning the masks on the conveyor belt. They also have fully established curing ovens and packaging processes to ensure no bottlenecks in delivery.