Ever pondering how to form complex vehicle parts like motor square, powertrain, and suspension components? Differentiate these bulky parts with lightweight components like surgical devices within the restorative industry. Pressure die casting, a prevalent fabricating handle, can fabricate this extent of items.
High-Pressure Die Casting Applications:
Due to the prevalent quality of items gotten through HPDC, the method has found different basic applications in a differing set of businesses. The Aviation Industry. Due to the capacity to fabricate complex and complex plans and mechanization, this process is exceedingly well known within the aviation industry. Amalgams of aluminum, zinc, and magnesium are utilized to fabricate motor parts for aviation applications. The Restorative Industry. It is additionally a prevalent method in creating lightweight surgical apparatuses within the therapeutic industry. Additionally, restorative gadgets and tall generation imaging gear, implantation pumps, etc., are moreover made utilizing the HPDC handle. The Car Industry. Huge pressure die casting can deliver different aluminum and magnesium car basic components. It makes parts such as motor squares, gearbox casings, oil sumps, motor mounts, and basic parts like cross-car pillars.
Why Using High-Pressure Die Casting Remains Great:
Huge pressure die casting may be a prevalent preparation in different businesses due to its few benefits relative to other fabricating forms. Underneath are a few of the points of interest. Great Quality Parts Fabricated. Other than that, high-pressure casting conveys great quality in terms of dimensional exactness and superior surface wrap-up. The high-precision items don’t require additional trimming forms which can get time-consuming and exorbitant. Great surface wrap-up facilitates the method of plating. Besides, the preferences of high-pressure pass-on casting items incorporate great consistency and ideal mechanical properties. Higher Generation Rates. Powerful pressure die casting comes about in higher generation rates than low weight or gravity casting. The utilization of tall weight empowers the infusion of liquid metal at tall speeds which come about at higher generation rates. Hence, making this handle well-known in high-volume fabrication.
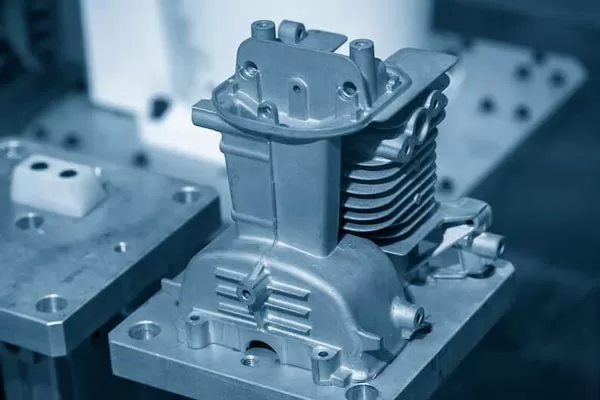
Pressure die casting part
More Ways to Use A High Pressure Die Casting Operation:
Accomplish Complex Plan. The pass-on casting handle permits the utilization of different kick the bucket shapes. Adaptability in pass-on shapes implies that complex parts can be delivered, amid the casting preparation, subsequently making a difference in complex congregations. The Lean Divider Products. The tall weights in this kick the bucket casting prepare can permit for more slender cross-sections than any other casting handle. Getting divider thicknesses beneath 0.40 mm is conceivable agreeing to your prerequisite and component measure. The lean dividers offer assistance in a weight decrease of the items. It moreover permits the expansion of embeds (moreover alluded to as “co-cast” parts) like screws and liners, inside the item amid the casting preparation. In this way, making a difference in diminishing the number of components amid gathering. Tough Passes on. The passes on utilized within the handle have a strong life expectancy which implies they can be reused in different generation cycles. This diminishes per unit fetched of the kick the bucket casting item.
The Working Process of High-Pressure Die Casting:
HPDC ordinarily works on the 4 forms of form planning, infusion, discharge, and post-casting treatment. There may be varieties within the strategy to cater to distinctive item necessities. These improvements incorporate vacuum pass on casting, slow-fill pass on casting, semisolid metal processing (SSM), etc. Trimming. The ultimate step of high pressure die casting includes the expulsion of additional fabric from the item and the shape. A trim pass on, saw, etc, can halo conduct the trimming preparation. In addition, the metal scraps can be reusable and recyclable in consequent generation cycles. Portion Expulsion. Upon guaranteeing that all the liquid metal has been set, evacuate the depression from the form.
Ejector pins can discharge the depth. The ejector pins are regularly included on the mobile conclusion of the form and thrust out the cemented casting portion from the depth. Infusion. Pour the liquid metal into a shot chamber, and after that infuse them into the form. There are 2 strategies whereby this infusion handle can happen. These are hot chamber and cold chamber infusion. Shape Planning. At the beginning of the generation cycle, it is vital to clean the kick the bucket cast shape to expel pollution. At that point, grease up the inside dividers of the form. This controls the mold’s temperature and permits for simple evacuation of the casted item.