Pressure Die Casting
Pressure die casting injects molten metal into steel molds under high pressure, producing precise, complex parts with minimal porosity. Widely used in industries like automotive and electronics for its efficiency and accuracy.
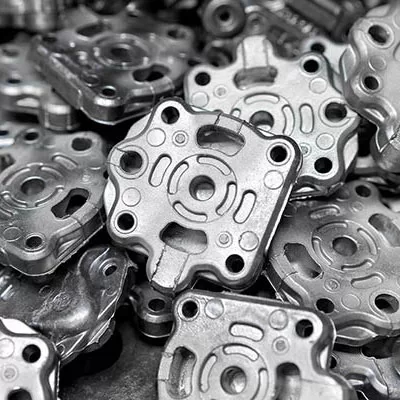
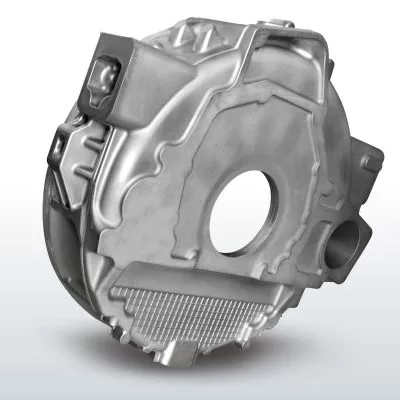
Precision Pressure Die Casting
NICE Rapid excels in delivering precision pressure die casting services, harnessing cutting-edge technology and expertise to fabricate metal components with unparalleled precision and quality. Our process involves injecting molten metal into meticulously crafted steel molds at pressures ranging from 1500 to 30,000 psi (10 to 200 MPa), ensuring precise replication of intricate details with minimal defects.
With a track record spanning various industries, including automotive, aerospace, electronics, and consumer goods, NICE Rapid has produced an extensive range of components, from engine blocks and housings to brackets and electronic enclosures. Our commitment to excellence is evident in our ability to achieve high dimensional accuracy, superior surface finish, and the capacity to manufacture complex geometries with tight tolerances.
At NICE Rapid, we understand the importance of meeting project requirements promptly and efficiently. Whether it’s rapid prototyping, small-batch production, or large-volume orders, our precision pressure die casting services are tailored to your needs, ensuring reliable, cost-effective, and high-quality solutions for your projects.
Advantages of Pressure Die Casting
Compare to other process, die casting has a significant advantage in cost-effective savings, especially for some components that has complex structure. It includes below other advantages:
Excellent dimensional accuracy.
Cast high strength sections within the structure directly.
Good surface finish compared to the other processes.
Reduction in material scrap.
Molds are built to last, enabling the production of thousands to millions of parts before replacement is necessary.
Applications
Here are the applications of pressure die casting summarized into four points.
Automotive and Aerospace
Used for engine components, transmission parts, structural components, and aircraft parts.
Electronics and Consumer Goods
Produces housings, connectors, enclosures, and decorative items for electronic devices and appliances.
Medical and Industrial Equipment
Provides components for medical devices, machinery, pumps, valves, and industrial equipment.
Energy and Defense
Utilized in renewable energy systems, traditional energy infrastructure, and defense applications for components like wind turbine parts, weapon components, and armor.
Ready to Start Your Next Project?
How Does Pressure Die Casting Work
Pressure die casting operates by injecting molten metal, typically aluminum, zinc, or magnesium alloys, into a precisely machined steel mold cavity at high pressure. This pressure ensures that the molten metal fills the entire cavity, including intricate details, before solidifying. Once solidified, the mold is opened, and the newly formed part, known as the casting, is ejected. This process allows for the rapid and cost-effective production of complex metal components with high dimensional accuracy and excellent surface finish. Additional post-processing steps may be applied to meet specific requirements, making pressure die casting a versatile and widely used manufacturing method across industries.
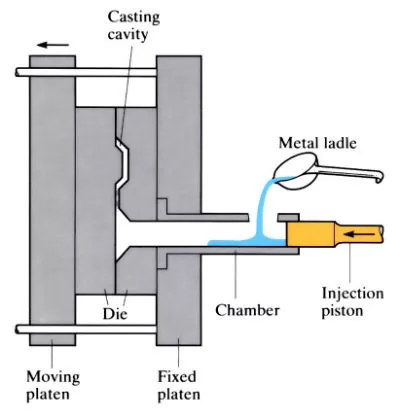
Surface Finishes for Pressure Die Casting
Pressure die casting produces parts with a relatively smooth surface, but additional finishing processes can be applied to enhance appearance, functionality, or durability. Common surface finishing techniques for pressure die castings include:
Selection Factors
The choice of finishing depends on:
-
Material
(Aluminum, Zinc, Magnesium alloys)
-
Application
(Decorative, wear-resistant, corrosion-resistant)
-
Cost & Production Volume
Mechanical Finishing
- Vibratory Finishing (Tumbling) – Uses abrasive media in a vibrating tub to deburr and polish surfaces.
- Sandblasting (Abrasive Blasting) – Projects fine abrasives (e.g., glass beads, aluminum oxide) to clean, texture, or prepare surfaces for coating.
- Grinding & Polishing – Manually or mechanically smoothens surfaces for a refined finish.
- Brushing – Uses wire or abrasive brushes to create a uniform grain texture.
Chemical Finishing
-
Acid Etching – Removes oxides and impurities while creating a matte or textured finish.
-
Chemical Brightening – Enhances surface shine using chemical baths (common for aluminum).
-
Passivation (for Zinc & Aluminum) – Improves corrosion resistance by removing free iron and forming a protective oxide layer.
Coating & Plating
-
Powder Coating – Electrostatic application of dry powder, cured under heat for a durable, decorative finish.
-
Electroplating – Deposits metals (e.g., nickel, chrome, zinc) for corrosion resistance and aesthetics.
-
Anodizing (for Aluminum) – Creates a hard, corrosion-resistant oxide layer, available in various colors.
-
E-Coating (Electrophoretic Coating) – Provides excellent corrosion protection with a uniform paint layer.
-
PVD (Physical Vapor Deposition) – Applies thin, wear-resistant metallic coatings (e.g., TiN, CrN).
Painting & Printing
-
Spray Painting – Adds color and protection with liquid or spray-applied paints.
-
Screen Printing/Pad Printing – Applies logos or markings for branding or identification.
Laser & Abrasive Finishing
-
Laser Engraving – Permanently marks parts with text, logos, or serial numbers.
-
Abrasive Flow Machining (AFM) – Polishes internal passages and complex geometries.