In the realm of modern manufacturing, few processes have revolutionized the production of plastic parts as significantly as injection molding. Injection molding stands as a cornerstone of mass production, offering unmatched precision, efficiency, and versatility. This article delves into the intricacies of injection molding, its applications, advantages, and its pivotal role in shaping various industries.
Understanding Injection Molding:
Injection molding is a manufacturing process that involves injecting molten material, typically thermoplastics or thermosetting polymers, into a mold cavity under high pressure. Once injected, the material solidifies within the mold, taking on its shape and intricacies. This process allows for the rapid and cost-effective production of complex plastic parts with consistent quality and dimensional accuracy.
The injection molding process comprises several essential components and stages:
Mold Design and Fabrication: The process begins with the design and fabrication of a mold, typically made of steel or aluminum, which defines the shape and features of the final part.
Material Preparation: Thermoplastic or thermosetting resin pellets are fed into a hopper and melted in a heated barrel, where they are compressed and injected into the mold cavity.
Injection: The molten material is injected into the mold cavity under high pressure, filling the space and taking on the precise shape of the mold.
Cooling: Once injected, the material undergoes a cooling process within the mold, during which it solidifies and forms the final part.
Ejection: After cooling, the mold opens, and the newly formed part is ejected from the cavity, ready for further processing or assembly.
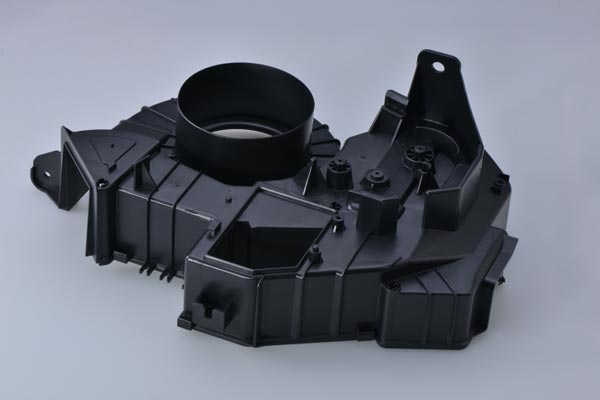
Plastic injection molded parts
Applications Across Industries:
Injection molding finds widespread application across a diverse range of industries, including automotive, electronics, medical, consumer goods, and packaging. In the automotive sector, injection molding is utilized for the production of interior components, exterior trim, and under-the-hood parts with tight tolerances and high durability.
In the electronics industry, injection molding is integral to the fabrication of housings, connectors, and enclosures for electronic devices, ensuring protection and reliability. Moreover, in the medical field, injection-molded parts such as syringes, IV components, and surgical instruments meet stringent requirements for biocompatibility, sterilization, and precision.
Advantages of Injection Molding:
The widespread adoption of injection molding is attributed to its numerous advantages:
High Efficiency: Injection molding enables high-volume production runs with minimal cycle times, leading to increased productivity and cost-effectiveness.
Precision and Consistency: Injection molding offers exceptional dimensional accuracy and repeatability, ensuring uniformity and consistency across parts.
Design Flexibility: The versatility of injection molding allows for the production of complex part geometries, intricate features, and undercuts, without the need for secondary operations.
Material Variety: A wide range of thermoplastic and thermosetting materials are available for injection molding, offering diverse mechanical properties, colors, and surface finishes to suit specific application requirements.
Sustainability: Injection molding promotes sustainability through material efficiency, waste reduction, and the ability to recycle or reuse scrap material generated during the manufacturing process.
Injection molding stands as a testament to the ingenuity and innovation of modern manufacturing, offering unparalleled precision, efficiency, and versatility in the production of plastic parts. From automotive and electronics to medical devices and beyond, injection molding continues to shape the products we use every day, driving progress and innovation across industries. As technology evolves and processes mature, injection molding remains a vital tool in the arsenal of manufacturers, enabling them to meet the demands of a rapidly changing world with confidence and precision.