Most CNC machined parts require finishing services to add to or alter their surfaces. These finishing techniques are used not only for aesthetic purposes but to improve the part or protect it from environmental impact.
It is a final step in CNC machining and most of these techniques can remove flaws, improve the appearance of the product, add strength and resistance, adjust its conductivity and many more. With all the finishing services available in the market today, how can you know which among them is the best one?
Fortunately, we have rounded up the most common finishes for CNC machined parts. Read this article to understand each of their unique advantages and how it applies to your requirement.
Types of Finishing Services for CNC Machined Parts
As-Machined Finish
CNC machined parts have a unique form of finishing known as “as-machined” or “as-milled” upon completing the process. The surface of these parts has minuscule but obvious tool marks and blemishes that can be tolerable. Its roughness is also acceptable as machined parts have tight tolerances where post-processing can be optional.
This type of finish is favorable for those who put more importance on the integrity of its dimensions instead of its aesthetics. What it is lacking is protection from the elements as they are susceptible to scratching, nicking, and scuffing.
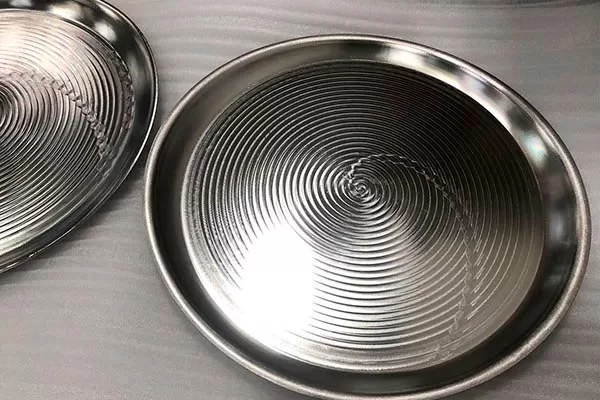
As Machined
Anodizing
Another finishing service that is popular with CNC machined parts is anodizing. It is an electrochemical process that adds thickness to the machined part’s inherent oxide layer. As a result, the machined part is more durable, electrically non-conductive, thicker, and denser.
Anodizing applies only to titanium and aluminum alloys as they conduct electricity well. During the process, the alloy is submerged in an acid electrolyte bath, which acts as an anode. When the cathode is placed in the anodizing tank and the electrical current conducts through the acid, the oxygen ions from the electrolyte and the atoms from the alloy combine and form at the surface.
Anodized finishes are durable and have good dimensional control. Most anodized parts are used in high-performance engineering applications, in particular for small parts and internal cavities. They also possess the most beautiful finishes but come at a high cost.
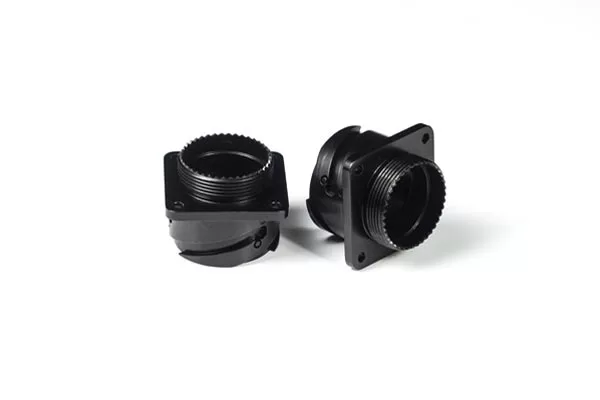
Anodizing parts
Powder Coating
Powder coating is equivalent to spray paint in CNC machined parts. The first step is priming the part using a chromating or phosphating coat to prevent corrosion. Then the part is painted using a dry painting coating from an electrostatic spray gun. The final step is curing the spray-painted part in an oven with 200 degrees temperature. In most instances, several layers of powder coating are applied to add thickness.
This finishing service adds a thin layer of protection to the CNC machined part to add strength, wear-resistance, and aesthetics. Compared with anodizing, this type of finishing applies to all metals. It is also less brittle and offers more impact resistance.
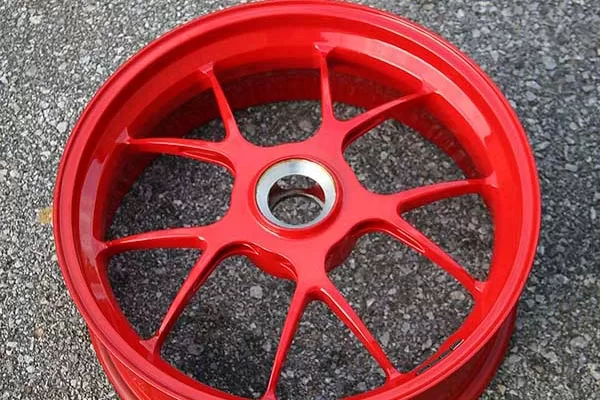
Powder coating red
Bead Blasting
This finishing service adds a satin or matte surface to a CNC machined part. In the process, the part is subjected to millions of beads shot from a pressurized air gun. As it goes, it evens out the surface from imperfections and tool marks, creating a grainy finish consistent throughout the surface.
Compared to anodizing and powder coating, bead blasting does not add any mechanical or chemical properties to the machined parts. Instead, it removes material from the part.
Bead blasting is the most affordable finishing service, but it needs an expert because the process is done manually.
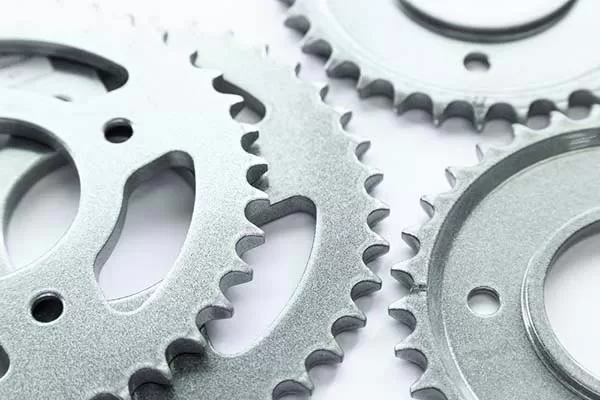
Bead blasting finishing parts
Conclusion
Finishing services like anodizing and powder coating can be the best option if the machined parts do not require a picture-perfect finish. However, if the part needs to be cost-effective and does not require a glossy finish, bead blasting is a great alternative.