Blow molding is a revolutionary process for producing containers, allowing various shapes and sizes to be created efficiently. This manufacturing technique enhances production speed and results in lightweight and durable containers that meet diverse industry needs. As you explore the intricacies of blow molding, you’ll gain insights into its applications and advantages.
Understanding the blow molding process can benefit businesses looking to innovate their packaging solutions. From beverage bottles to cosmetic containers, this method ensures that products are functional and visually appealing. The versatility of blow molding makes it a preferred choice for many manufacturers aiming to optimize their operations.
If you’re considering blow molding for containers, learning about the different types of blow molding processes available and how they impact your end product is essential. This knowledge can set your packaging apart in a competitive market, making your products more attractive to consumers.
Fundamentals of Blow Molding
Blow molding is a widely used manufacturing process for creating hollow plastic containers. Understanding its history, basic methods, and the types of machines involved provides valuable insight into its applications and advantages.
History and Evolution
Blow molding dates back to the early 20th century, when it was primarily used for glass manufacturing. The first blow molding machine for plastics was patented in the 1930s, which transformed the production of various containers.
Initially, this method was limited to several materials, mainly thermoplastics. Over the decades, technological advancements enhanced the process, allowing for greater efficiency and flexibility in design. By the 1980s, it became a favored choice for producing items like bottles and automotive parts due to its speed and cost-effectiveness.
Basic Process Overview
The blow molding involves three key steps: extruding, molding, and cooling. First, a thermoplastic material is heated until it becomes malleable.
Next, this material is formed into a parison, a hollow tube shape. The parison is then placed in a mold, and air is blown into it, expanding the plastic to fill the mold’s cavity.
After cooling, the finished product is ejected from the mold. This method allows for large production runs of identical pieces, reducing waste and production time, making it efficient for large-scale manufacturing.
Types of Blow Molding Machines
There are three main types of blow molding machines: extrusion, injection, and stretch blow molding.
- Extrusion Blow Molding: This is the most common type, in which the part is formed from a heated plastic tube. It’s ideal for creating large containers.
- Injection Blow Molding: In this process, the plastic is first injection molded into a pre-form. The preform is then blown into shape, providing precise control over wall thickness.
- Stretch Blow Molding: This method uses preforms as well, but they are stretched during the blowing process, enhancing the final product’s strength and clarity.
Each type of machine offers unique advantages, permitting manufacturers to select the best option based on their specific needs.
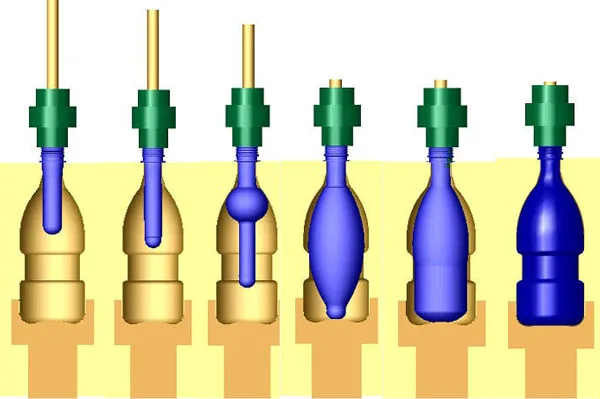
Injection blow molding
Container Design and Manufacturing
Effective container design and manufacturing are crucial in the blow molding process. Key aspects such as material selection, shapes and features, mold design, and production workflow are significant in creating functional and aesthetically pleasing containers.
Material Selection
Choosing the right material for your containers is essential for durability, function, and cost-effectiveness. Common materials used in blow molding include polyethylene (PE), polypropylene (PP), and polyvinyl chloride (PVC). Each material has specific properties: PE is flexible and impact-resistant, while PP offers excellent chemical resistance.
Factors such as container application, required strength, and environmental conditions should influence your choice. Consideration of recyclability is also essential as sustainable practices become increasingly prioritized. Always consult material suppliers for the latest innovations to enhance your container’s performance.
Container Shapes and Features
The shape of your container directly affects its functionality, storage, and transportation. Blow molding allows for the creation of complex shapes, including round, square, and custom designs. Each shape can serve a different purpose—round containers are commonly used for liquids, while rectangular versions often optimize shelf space.
Features like handles, spouts, or unique closures can enhance user experience and meet specific market demands. To make your product stand out, you can also consider aesthetic elements, such as surface textures or colors.
Mold Design Considerations
Mold design is a critical component that impacts the efficiency and quality of production. High-quality molds are crafted from materials like aluminum or steel, which provide durability and precision. Features like cooling channels and mold venting systems help optimize cooling time and maintain container integrity.
It’s vital to collaborate with experienced mold designers to ensure your mold meets the specifications of your container. Your mold must facilitate easy release, consistent wall thickness, and accommodate any specific shapes or features you’ve designed.
Production Workflow
A well-structured production workflow ensures efficiency from start to finish. The process begins with material preparation, where resin is melted and molded into parisons. These parisons are then inflated using air into the desired container shape.
Implementing quality control at various stages, from material selection to final inspection, helps maintain standards. Investing in automated systems can also enhance output while minimizing errors. Ensuring a seamless workflow can lead to timely production and reduced costs, benefiting your project significantly.
For precise design and manufacturing, consider reaching out to Nicerapid.com. They offer expert services and can provide a quote tailored to your project needs.