Speed and efficiency are critical in today’s fast-paced manufacturing environment. Rapid tooling has emerged as a game-changing technology that bridges the gap between prototyping and full-scale production. Unlike traditional tooling methods, which can take weeks or months to develop, rapid tooling enables manufacturers to produce molds quickly and cost-effectively, accelerating product development cycles.
What is Rapid Tooling?
Rapid tooling refers to the fast production of molds and dies using advanced manufacturing techniques such as 3D printing (additive manufacturing), CNC machining, and soft tooling. These methods allow for faster turnaround times compared to regular steel or aluminum tooling, making them ideal for:
- Prototyping – testing part designs before mass production
- Low-volume production – manufacturing small batches of parts
- Bridge tooling – temporary molds used before investing in hard tooling
Types of Rapid Tooling
There are two main categories of rapid tooling:
1. Direct Rapid Tooling
In this method, the mold itself is produced using additive manufacturing or high-speed machining. Examples include:
3D-printed molds – Made from resins, metals, or composite materials using technologies like SLA, DMLS, or binder jetting.
CNC-machined molds – Faster than traditional machining but typically made from softer metals like aluminum.
Best for: Short-run production and functional prototypes.
2. Indirect Rapid Tooling
Instead of making the final mold directly, a master pattern is created (often via 3D printing), which is then used to produce a mold through processes like:
Silicon molding (Room Temperature Vulcanization – RTV) – Used for soft, flexible molds.
Epoxy or composite tooling – Reinforced molds for low-pressure injection molding.
Investment casting patterns – For creating metal molds via lost-wax casting.
Best for: Complex geometries and medium-volume production.
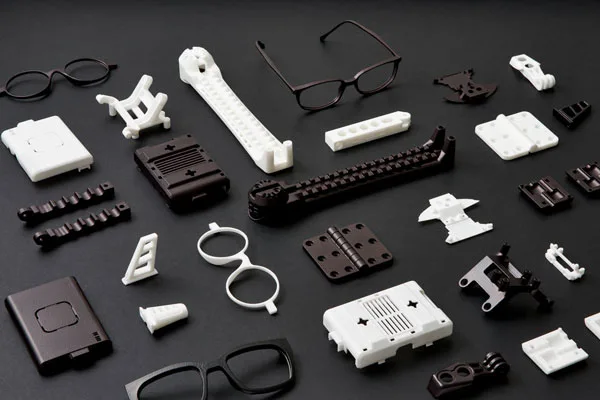
3D printing parts
Key Benefits of Rapid Tooling
- Faster Time-to-Market
Traditional tooling can take 8–12 weeks, while rapid tooling reduces this to days or weeks, allowing companies to iterate designs quickly.
- Lower Costs for Prototyping & Small Batches
Hard steel molds are expensive, making them impractical for prototypes. Rapid tooling offers an affordable alternative to test designs before committing to high-cost production tooling.
- Design Flexibility & Iteration
Engineers can easily modify digital designs and produce new molds without the high costs of traditional tooling changes.
- Enables Low-Volume Production
Start-ups and niche manufacturers can produce small batches economically without a large upfront investment.
- Supports Complex Geometries
Additive manufacturing allows for intricate mold designs that would be difficult or impossible with conventional machining.
Applications of Rapid Tooling
Automotive Industry
Prototyping interior components, air ducts, and under-the-hood parts. Low-volume production of custom or aftermarket parts.
Medical Devices
Fast production of surgical tools, housings, and biocompatible components. Customized prosthetics and dental molds.
Consumer Electronics
Rapid prototyping of casings, buttons, and connectors. Short-run production before mass manufacturing.
Aerospace
Lightweight components with complex internal structures. Functional testing of ducting and structural parts.
The Future of Rapid Tooling
Advances in 3D printed materials, hybrid manufacturing, and AI-driven design optimization are pushing rapid tooling to new levels. Key developments include:
- High-performance 3D-printed metal molds-increased durability for longer production runs.
- Conformal cooling channels-3D printed molds with optimized cooling for faster cycle times.
- Automated mold design software – AI-powered tools that optimize mold geometry for efficiency.
As these technologies mature, rapid tooling will become even more integral to agile manufacturing.
Conclusion
Rapid tooling is transforming product development by enabling faster, more flexible production of molds and prototypes. Using 3D printing and additive manufacturing, companies can now create tools in days rather than weeks, allowing for faster design validation and iteration.
This approach not only speeds up prototyping, but also ensures that the test parts closely match the final product in form and function. As 3D printing and hybrid manufacturing continue to advance, rapid tooling will further shorten development cycles, improve test accuracy, and optimize production efficiency-making it a key driver of innovation in modern manufacturing.