Pressure die casting is an essential manufacturing process tailored to produce intricate aerospace components with precision and efficiency. This method excels in creating lightweight, high-strength parts that meet the industry’s rigorous standards. In demand for advanced materials and reduced production times, pressure die casting offers an effective solution for meeting these challenges.
The need for reliability and performance in aerospace applications cannot be overstated. Pressure die casting ensures that your components are durable and capable of withstanding extreme operating conditions. The technology allows for precise control over the casting process, producing complex geometries that enhance structural integrity while minimizing waste.
As you explore pressure die casting for aerospace parts, you’ll discover the benefits of integrating this technique into your production strategy. From cost-effectiveness to improved material properties, understanding its advantages can significantly impact your operational success in the aerospace sector.
Basics of Pressure Die Casting
Pressure die casting is a sophisticated manufacturing process widely used for producing high-precision aerospace components. This process involves forcing molten metal into a mold under high pressure, ensuring that parts have excellent dimensional accuracy and surface finish.
Definition and Principles
Pressure die casting is a manufacturing method that injects molten metal into a mold cavity at high pressure. This technique results in excellent detail and surface quality in the final product. The process relies on two key principles: fast solidification and the ability to produce complex geometries. The quick cooling of the metal in the mold leads to a fine microstructure, enhancing mechanical properties essential for aerospace applications.
Materials and Alloys Used
The choice of materials in pressure die casting is crucial for aerospace parts. Common alloys include:
- Aluminum Alloys: Known for their light weight and high strength, these alloys are widely used in aerospace components.
- Zinc alloys: These offer good fluidity and yield higher-strength parts than aluminum in some applications.
- Magnesium Alloys: Lightweight and strong, these alloys contribute to weight reduction and structural integrity.
Each material is selected based on the specific requirements of the aerospace application, including temperature tolerance and corrosion resistance.
Machinery and Equipment
The machinery involved in pressure die casting is specialized and designed for high efficiency. Key components include:
- Die Casting Machines: These machines can apply substantial pressure to inject molten metal quickly.
- Molds: Precision-engineered molds are critical for achieving the desired shape and finish. They are often made from hardened steel to withstand repeated use.
- Heating and Cooling Systems: These systems regulate the temperature of the molten metal and mold, ensuring optimal solidification rates.
Selecting the right machinery and maintaining it properly is vital for producing aerospace parts that meet rigorous industry standards.
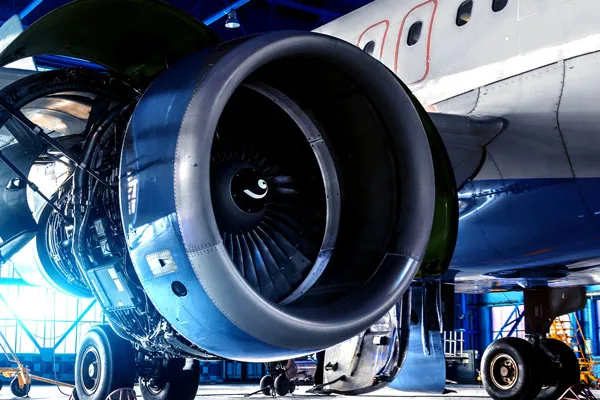
Aerospace aluminium alloys
Pressure Die Casting in the Aerospace Industry
Due to its efficiency and precision, pressure die casting is increasingly essential in the aerospace sector. This process allows the creation of complex geometries while meeting the exacting standards required for aircraft components. Understanding its advantages, design considerations, quality control measures, and real-world applications can significantly enhance your manufacturing strategy for aerospace parts.
Advantages for Aerospace Applications
Pressure die casting offers numerous benefits tailored to aerospace needs. The process enables the production of lightweight components that can withstand high stress and strain, which is crucial for aircraft performance.
Some key advantages include:
- Material Efficiency: Near-net shape technology helps minimize waste.
- Dimensional Accuracy: Produces parts with tight tolerances, reducing the need for extensive machining.
- Surface Finish: Provides a smooth surface, which is essential for both aerodynamics and aesthetics.
These features minimize production costs and improve lead times, vital in the competitive aerospace market.
Design Considerations
In aerospace applications, design intricacies must align with the die-casting process. Components should incorporate features that facilitate the casting, such as removing undercuts and using uniform wall thickness.
Key design tips include:
- Draft Angles: Essential for easy mold extraction.
- Ribbing: Increases strength without adding excessive weight.
- Mate Location Features: Aid in assembly and alignment.
Collaboration with engineers during the design phase ensures that the final product meets regulatory standards while optimizing performance.
Quality Control and Standards
Aerospace components must adhere to stringent quality standards. Implementing rigorous quality control measures throughout the pressure die casting process can prevent defects and ensure reliability.
Key quality control measures include:
- Non-Destructive Testing (NDT): Techniques like X-ray or ultrasonic testing reveal internal flaws.
- Dimensional Inspection: Ensures that parts meet specified tolerances.
- Material Certification: Confirms that materials used comply with aerospace specifications.
Staying compliant with standards such as AS9100 can enhance customer trust and reduce the risk of failure in critical applications.
Case Studies and Real-World Examples
Numerous aerospace companies leverage pressure die casting to optimize their production. For instance, producing turbine housings and structural components showcases the process’s efficiency.
A notable example is the use of aluminum die casting to create lightweight brackets that meet FAA standards. These parts benefited from a substantial weight reduction, enhancing fuel efficiency and performance.
Collaboration with specialized manufacturers can lead to successful case studies, illustrating the feasibility and advantages of this casting method.
For your aerospace projects, consider contacting Nicerapid.com. They offer professional insights and quotes tailored to your specific requirements.