Rapid Tooling
DFM Reports and Mold Flow Analysis
Low Cost Fast Delivery
One stop Tooling Solutions
Precision Rapid Tooling Services
At Nice Rapid, we offer a wide range of manufacturing services and solutions for all your rapid tooling needs. From your design concept to creation, all of your designs and ideas are created efficiently and securely in our shop, it’s a one-stop for everything providing you with the ultimate class and convenience.
Our center of production is quite spacious giving our engineering and design team ample space to work on your project in an efficient and free manner. Our production and sales team work hand in hand thus ensuring that the final end-products match the original designs and ideas. Our rapid tooling services are tailor-made to provide you with quality injection molded parts within the shortest time possible. Additionally, the confirmation process of all your designs will be fastened giving you a picture of the final injection molded parts using your preferred material. Learn more about our plastic injection molding services.
Rapid tooling is one of the quickest and fastest ways of production compared to the tooling process, this is partly attributed to the efficient ways in which the CAD designs are produced. Additionally, rapid tooling also involves smaller volumes making it an effective and efficient way. After we receive the CAD files, we will send you the samples within 15-days. This is just a rough estimate it can even be shorter than the set time limit, the efficiency and effectiveness of the design tool can result in larger production cycles using the same tool which will not only reduce production cost but also improve on efficiencies.
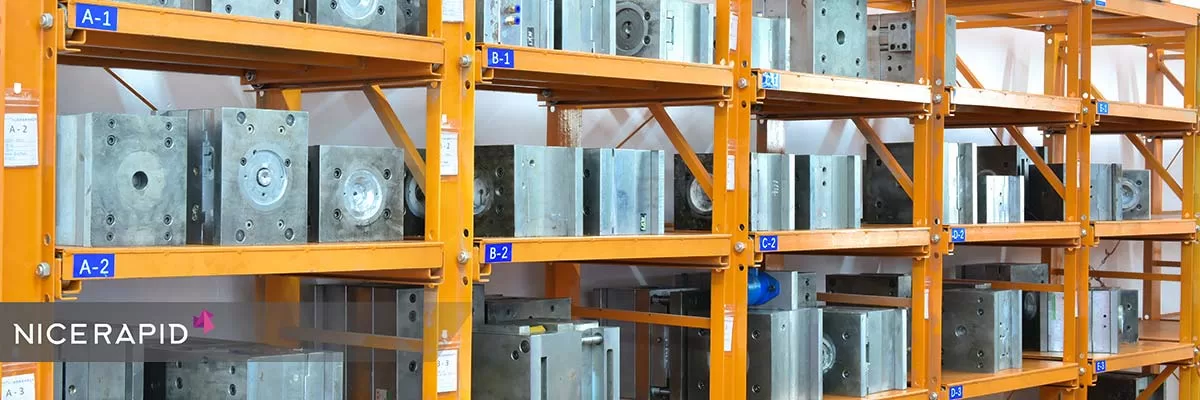
Common Types of Rapid Tooling
Aluminum Mold Tooling and Steel Mold Tooling
The enduring debate between aluminum and steel as the superior material in terms of longevity and cost-effectiveness remains a perennial topic. At our company, we take pride in delivering top-notch services to our clients, which is why we aim to shed light on this ongoing discussion. With our extensive experience, we’ve observed that steel has traditionally been the preferred choice for most rapid tooling projects due to its durability. However, recent fluctuations in steel prices have prompted a shift in favor of aluminum. Apart from its cost advantage, aluminum boasts quicker production times, spearheading a revolution in rapid tooling. At Nice Rapid, we stand at the forefront of this evolution. Below, we present a concise comparison between these two remarkable materials.
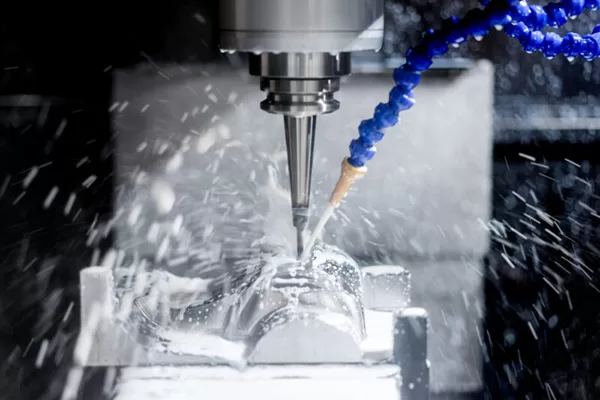
Aluminum Mold Tooling
Suitable for complex parts
Large pool for surface finish options
Easy to modify
Less flash and over-weld
Cost-effective and long-lasting
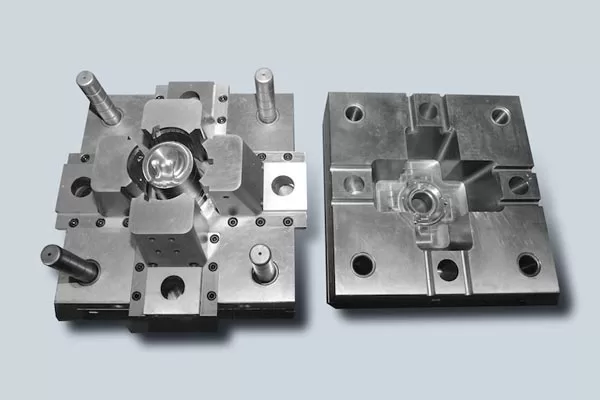
Steel Mold Tooling
Faster production times
Easy to store and move
Low cost of production
Heat transfer faster
Light weight
From the above discussion, the selection of the two materials the quantity and the part/product being manufactured. At Nice Rapid we will factor in the two aspects and advice you accordingly on which is the best material, we also specialize in using the two materials to their fullest potential.
Rapid Tooling Resources
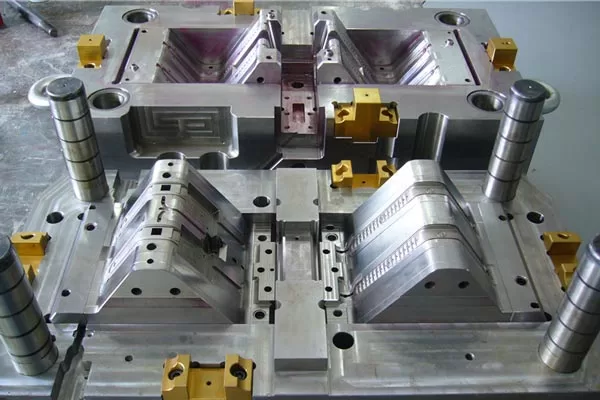
Top Five Tips for Molding Design
This article provides essential guidelines for achieving optimal results in rapid tooling and injection molding projects. It covers critical aspects such as process optimization, wall thickness, draft angles, texture integration, and material selection, ensuring efficient production and high-quality outcomes.
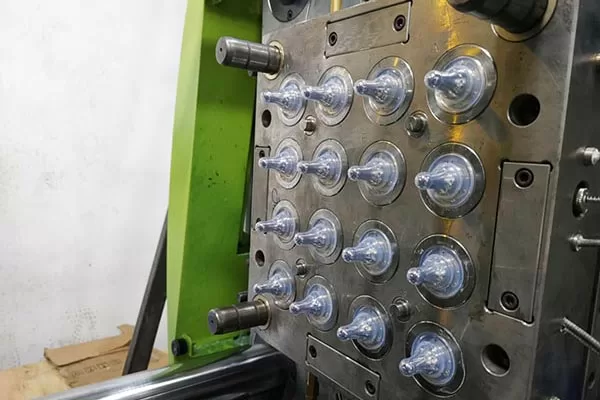
Family Moulds – The Lowdown
This articles explores the advantages and challenges of using family molds in injection molding. It discusses key considerations such as resin flow, gate design, and side actions to ensure optimal production efficiency and quality. The post emphasizes the importance of consulting professionals to determine the suitability of family molds for specific projects.
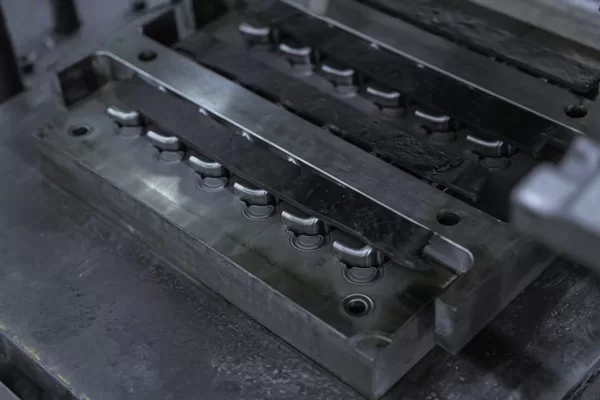
The Importance of DFM Report for Rapid Tooling
It outlines the role of Design for Manufacturability (DFM) in streamlining the transition from prototyping to production. It highlights DFM’s benefits, including cost reduction, enhanced efficiency, and improved product quality. The post also details key DFM principles and processes to optimize manufacturing outcomes in rapid tooling projects.