Plastic Injection Molding Surface Finishes
Plastic injection molded parts can be surface finished from matte to highly polished. The higher requirement on the surface finish of the part, the longer effort and time spent during the production of the mold, hence it will lead to higher cost on your overall cost.
Understanding your surface requirement is very important, as sometimes it’s unnecessary to polish your part that is for internal use only and not for the aesthetic purposes. Hence, identifying the right surface finish is very important and dependent on few key elements, which are during different stage of product development, the material used and their end-use applications.
Surface Finishes and the Common Standards
Plastic injection molded parts are not usually undergone secondary surface finishing, but the mold itself can be surface finished to various degrees.
Rough surfaces will increase the friction between the part and the mold during the ejection. Hence a larger draft angle is required.
There are several surface finishes standards that commonly referred by the product designers or manufacturers in plastic injection molding industry which are:
- SPI (Society of Plastic Industry)
- Mold-Tech
- VDI (Verein Deutscher Ingenieure), the society of German Engineers
1. SPI
The Society of Plastic Industry (SPI) explains several standard-finishing procedures and their corresponding resulted surface finishes.
Finish |
Mold Finish Description |
Description |
SPI Standard |
Comments |
Surface Roughness, Ra(um) |
Glossy |
#3 Diamond Polish |
The mold is first smoothed and then polished with a diamond buff. |
A-1 |
Mirror-like Finish |
0 – 1 |
#6 Diamond Polish |
A-2 |
1 – 2 |
|||
#15 Diamond Polish |
A-3 |
2 – 3 |
|||
Semi-Glossy |
#600 Grit Paper |
The mold is smoothed with fine grit paper. |
B-1 |
Fine surface Finish |
2 – 3 |
#400 Grit Paper |
B-2 |
4 – 5 |
|||
#320 Grit Paper |
B-3 |
9 – 10 |
|||
Matte |
#600 Grit Stone |
The mold is smoothed with fine grit stone. |
C-1 |
Removing all machining marks |
10 – 12 |
#400 Grit Stone |
C-2 |
25 – 28 |
|||
#320 Grit Stone |
C-3 |
38 – 42 |
|||
Textured |
#11 Glass Bead |
The mold is first smoothed with fine grit stone and then sandblasted with different medias. |
D-1 |
Resulting in a textured surface. |
10 – 12 |
#240 Aluminium Oxide |
D-2 |
26 – 32 |
|||
#24 Aluminium Oxide |
D-3 |
190 – 230 |
|||
As-Machined |
– |
The mold is finished to the machinist’s discretion. |
– |
Visible tool marks |
Canbe down to 0.8 or up to 32 |
SPI Reference
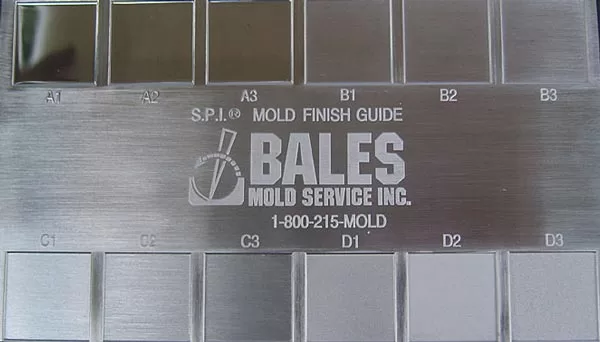
2. Mold-Tech
Below are the series of Mold-Tech texture specifications and their corresponding texture depth and draft angle specification that commonly used as the surface finish reference in plastic injection molding.
Mold-Tech A |
|
Mold-Tech B |
||||
Pattern # |
Depth (mm) |
Draft Angle (min) |
|
Pattern # |
Depth (mm) |
Draft Angle (min) |
MT-11000 |
0.01016 |
1˚ |
|
MT-11200 |
0.07620 |
4.5˚ |
MT-11010 |
0.02540 |
1.5˚ |
|
MT-11205 |
0.06350 |
4˚ |
MT-11020 |
0.03810 |
2.5˚ |
|
MT-11210 |
0.08890 |
5.5˚ |
MT-11030 |
0.05080 |
3˚ |
|
MT-11215 |
0.11430 |
6.5˚ |
MT-11040 |
0.07620 |
4.5˚ |
|
MT-11220 |
0.12700 |
7.5˚ |
MT-11050 |
0.11430 |
6.5˚ |
|
MT-11225 |
0.11430 |
6.5˚ |
Please note that the above draft angles are for reference only. Part geometry, molding materials, texture construction and molding process parameter all have impact on draft angle. The actual draft angle need to be analyzed by manufacturer based on case-by-case basis.
Mold-Tech Reference
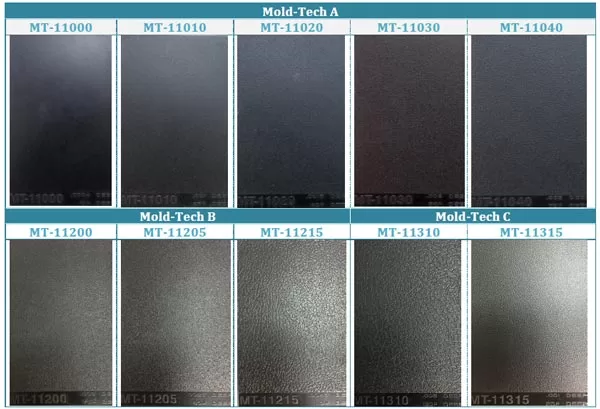
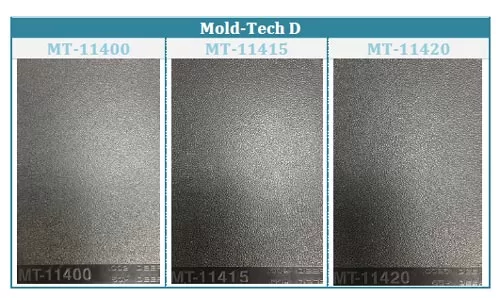
3. VDI
VDI surface finishes refers to texture standard set by Verein Deutshcher Ingenieure (VDI), the Society of German Engineers. It is generally produced using EDM (Electrical Discharge Machining) process when machining the mold. They can also be created using comparable “Mold-Tech” style finishes. EDM is used for smaller areas and “Mold-Tech” is generally for large areas.
VDI |
Draft angle – °per side |
||||
VDI # |
Ra (um) |
Rz (um) |
ABS |
PC |
PA (Nylon) |
12 |
0.4 |
1.5 |
0.5˚ |
1˚ |
0˚ |
15 |
0.56 |
2.4 |
0.5˚ |
1˚ |
0.5˚ |
18 |
0.8 |
3.3 |
0.5˚ |
1˚ |
0.5˚ |
21 |
1.12 |
4.7 |
0.5˚ |
1˚ |
0.5˚ |
24 |
1.6 |
6.5 |
1˚ |
1.5˚ |
0.5˚ |
27 |
2.24 |
10.5 |
1.5˚ |
2˚ |
1˚ |
30 |
3.15 |
12.5 |
2˚ |
2˚ |
1.5˚ |
33 |
4.5 |
17.5 |
2.5˚ |
3˚ |
2˚ |
36 |
6.3 |
24 |
3˚ |
4˚ |
2.5˚ |
39 |
9 |
34 |
4˚ |
5˚ |
3˚ |
42 |
12.5 |
48 |
5˚ |
6˚ |
4˚ |
45 |
18 |
69 |
6˚ |
7˚ |
5˚ |
Please bear in mind that the above draft angles are for reference only. It varies based on case-by-case basis and will be increased by taking all variables into consideration, such as part design (thin wall, deep cores, cutoff, etc), molding process parameter and material used (e.g. glass filled material will require more draft angle).
VDI Reference
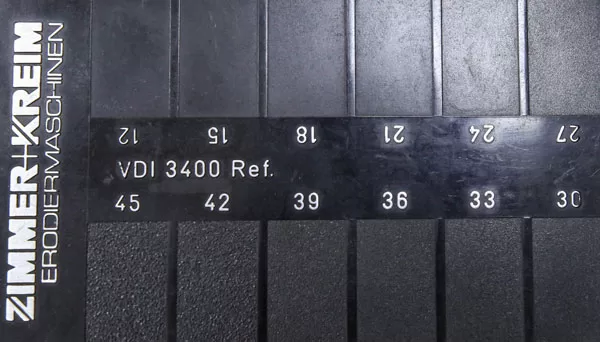
Useful Tips on Surface Finish Selection
A high glossy mold finish is not equivalent to a high glossy injection molded part. This is all dependent on other factors such as material used, molding condition, mold and part design. For example, ABS part has higher glossy surface finish than PP.
High glossy surface finish requires a higher grade of mold material. In order to achieve a very fine polished surface finish, tool steels with the highest hardness are required. For example, NAK80 tool steel (HRC 40- 43) is required to produce SPI A2 mirror-like surface finish instead of P20 (HRC 30-33). Please bear in mind that higher hardness of mold tool will increase the machining time and post-processing time, which will impact on the overall cost and lead time.
Glass or other mineral-filled materials can create material streaking and will be harder to produce highly cosmetic part. However, this is not always the case. Always speak to manufacturer to obtain a material sample plaque of the actual material you intend to use to have a better view of what surface requirement you are after.