Blow molding produces hollow plastic products by inflating heated plastic material inside a mold. This process creates everything from bottles to complex automotive components with consistent wall thickness.
Understanding the Blow Molding Manufacturing Process
The blow molding process begins with creating a parison, also known as a preform. This hollow tube of heated plastic serves as the starting material for the final product.
Air pressure inflates the parison against the mold walls. The plastic takes the shape of the mold cavity while maintaining its hollow interior.
Cooling solidifies the plastic in its final form. The mold opens, and the finished part gets ejected automatically.
Three main blow molding types exist: extrusion, injection, and stretch blow molding. Each method suits different product requirements and production volumes.
Types of Blow Molding Techniques Explained
Extrusion blow molding works best for large containers and irregularly shaped products. The continuous extrusion process allows for varying wall thickness.
Injection blow molding produces smaller, precision bottles with consistent wall thickness. This method offers superior dimensional control and surface finish quality.
Stretch blow molding creates bottles with enhanced clarity and strength. The stretching process orients the plastic molecules for improved performance.
Rotational blow molding forms large, complex hollow products. This method is particularly effective for tanks, playground equipment, and automotive fuel tanks.
Applications Where Blow Molding Excels
The packaging industry relies heavily on blow molding for bottles and containers. Water bottles, detergent containers, and food packaging all use this process.
Automotive components include fuel tanks, air ducts, and fluid reservoirs. The lightweight nature of blow-molded parts improves vehicle fuel economy.
Toys and sporting goods benefit from the hollow construction that blow molding provides. Beach balls, kayaks, and large toy figures use this manufacturing method.
Industrial applications include chemical tanks, shipping containers, and equipment housings. The chemical resistance of molded plastics makes them suitable for harsh environments.
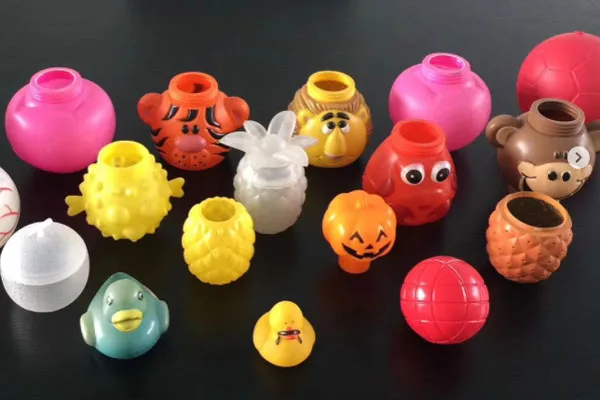
Blow molding toys
Material Selection for Blow Molding Success
Polyethylene dominates blow molding applications due to its processability and chemical resistance. Both high-density and low-density versions work well.
Polypropylene offers higher temperature resistance and clarity. Food containers and medical applications often specify this material.
PET provides excellent clarity and barrier properties. Beverage bottles almost exclusively use PET through the process of stretch blow molding.
Specialty materials include multilayer structures and barrier resins. These materials extend shelf life and provide specific performance characteristics.
Design Guidelines for Optimal Results
Uniform wall thickness prevents weak spots and material waste. Design features should promote even material distribution during the forming process.
Parting line placement affects both appearance and structural integrity. Strategic placement minimizes visible seam lines on finished products.
Handle and grip integration requires careful material flow planning. These features must form properly without creating stress concentrations.
Threading and closure compatibility demands precise dimensional control. Proper mold design ensures consistent thread formation.
Maximizing Your Hollow Product Manufacturing
Production speed depends on part size and cooling requirements. Smaller parts cycle faster but may require multi-cavity tooling.
Quality control focuses on measuring wall thickness and verifying dimensions. Consistent monitoring prevents defective products from reaching customers.
Tooling maintenance affects both part quality and production uptime. Regular cleaning and inspection extend the life of the mold and maintain precision.
Ready to bring your hollow plastic product ideas to reality? Contact Nice Rapid to explore our comprehensive blow molding capabilities and discover how our outsourcing services can streamline your manufacturing process while maintaining the highest quality standards.