Pressure die casting creates complex metal parts through a high-pressure injection process. This manufacturing method produces components with excellent dimensional accuracy and smooth surface finishes.
How Pressure Die Casting Delivers Superior Results
The pressure die casting process forces molten metal into a steel mold under extreme pressure. This pressure ranges from 1,500 to 25,000 PSI, ensuring complete cavity filling.
Rapid cooling solidifies the metal quickly, resulting in fine-grained structures. These structures provide superior mechanical properties compared to sand casting methods.
Two main pressure die casting variations exist: hot chamber and cold chamber processes. The hot chamber works best with low-melting-point metals, such as zinc and magnesium.
Cold chamber pressure die casting handles higher-melting-point metals, including aluminum and copper alloys. The metal melts separately before injection into the die.
Material Options for Pressure Die Casting Applications
Aluminum alloys dominate pressure die casting applications. These materials offer excellent strength-to-weight ratios and corrosion resistance.
Zinc alloys provide superior dimensional accuracy and surface finish quality. They also offer excellent electrical conductivity for electronic applications.
Magnesium alloys deliver the lightest weight options available. Automotive applications benefit from magnesium’s vibration-damping properties.
Copper alloys bring high thermal and electrical conductivity. Plumbing fixtures and electrical components often use copper-based pressure die casting.
Industries That Rely on Pressure Die Casting
- Automotive manufacturing uses pressure die casting for engine blocks, transmission housings, and structural components. The process creates parts that withstand high stress and temperature conditions.
- The electronics industry depends on die-cast housings for computers, phones, and appliances. The electromagnetic shielding properties protect sensitive components.
- Hardware and tools benefit from the strength and durability of die-cast components. Power tool housings and hand tool parts use this manufacturing method.
- Aerospace applications require the lightweight strength that pressure die casting provides. Aircraft components must meet strict weight and performance standards.
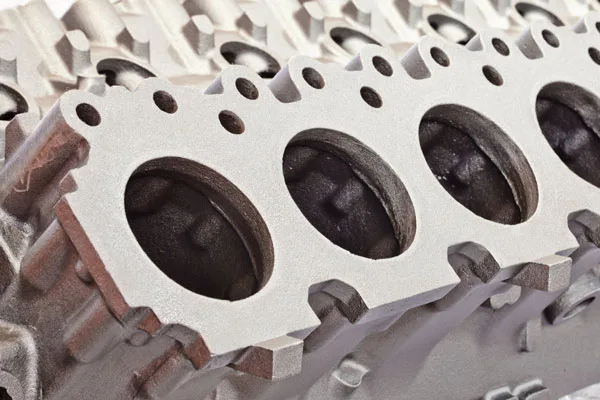
Die cast engine block
Design Considerations That Maximize Success
Wall thickness affects both part quality and production costs. Uniform thickness prevents internal porosity and reduces cycle times.
Draft angles enable easy part removal from the die. An insufficient draft can damage both the part and the tooling.
Fillet radii strengthen corners and reduce stress concentrations. Sharp corners create weak points that may fail under load.
Undercuts complicate die design and increase tooling costs. Redesigning parts to eliminate undercuts often reduces overall manufacturing expenses.
Optimizing Your Metal Component Production
Production volumes determine tooling investment levels. High-volume projects justify more expensive but durable die construction.
Tolerance requirements influence both die design and production processes. Tighter tolerances may require secondary operations.
Surface finish specifications affect die surface preparation and maintenance schedules. Polished dies produce superior part finishes.
Looking to harness the power of pressure die casting for your metal components? Nice Rapid specializes in delivering high-quality die casting solutions through comprehensive outsourcing services that meet your exact specifications and timeline requirements.