Die casting offers an efficient and accurate process for rapid prototyping. The metallic manufacturing process suits consumer, commercial, and industrial projects. Die-casting tooling has plenty of longevity, making it suitable for manufacturing complex components while reducing costs for mass manufacturing.
Die metal casting works with several materials, usually non-ferrous metals with minimal iron content. However, some manufacturing partners are capable of processing ferrous metals as well.
The most popular materials for metal die casting include zinc, magnesium, and aluminum alloys. Each has different grades, offering advantages for specific applications. This post unpacks the grades of these popular materials.
Metal Die Casting Explained
Die casting is a manufacturing process implementing the casting of molten metals. The process involves pouring or forcing liquid metal into a mold cavity, where it cools and forms the shape of the die. Investment casting and sand casting are examples of other die manufacturing processes. Each offers unique advantages, like low or high-volume production or cost savings.
Casting methods differ between mold and pattern types, materials, and delivery methods, such as high-pressure injection or gravity pouring. Die-casting processes are particularly useful for the high-volume production of complex components and low-volume prototyping projects, bringing versatility to its manufacturing applications.
A metal die utilizes two steel dies to create a permanent mold. Typically, these dies are manufactured using CNC machining processes for optimal accuracy and precision. However, they are incredibly expensive to make and take a while to manufacture.
However, the die has a long shelf-life, being one of the most durable options for prototyping projects and mass-production requirements. Many industries rely on metal die casting for component production across industrial, commercial, and consumer products.
If we compare this method to other metal casting strategies, it’s best suited for manufacturing small to mid-sized components requiring a high-quality surface finish.
Considerations for Choosing the Right Die Casting Materials
When choosing the right materials for die-casting projects, die manufacturers should consider the following variables.
- Is the material compatible with “hot-chamber” casting?
- What are the costs of the materials used in the project?
- What are the processing times for the materials?
- What are the material’s structural properties regarding weight, strength, finish, and machinability?
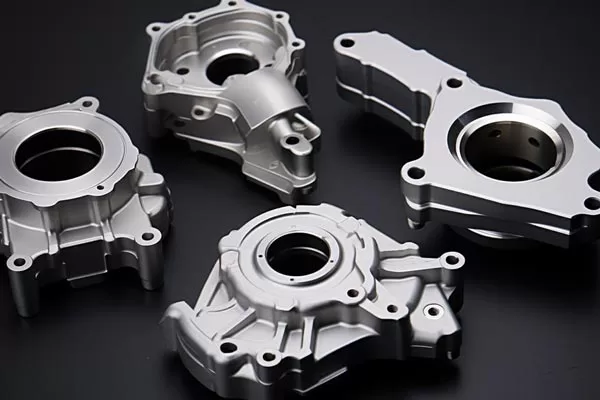
Aluminium die casting
Popular Aluminum Die Casting Materials
Aluminum is the most popular metal for die-casting projects. Aluminum alloy is ideal for “cold chamber” die-casting projects. These aluminum alloys typically feature materials like magnesium, copper, or silicon.
Aluminum is lightweight, making it ideal for larger die-casting projects. The material offers exceptional dimensional stability, making the alloys a great choice for manufacturing intricate components.
This material offers excellent resistance to temperature fluctuations and corrosion while offering good electrical and thermal conductivity. Aluminum comes in different grades, each offering unique properties for die-casting projects. Let’s look at each of them in detail.
- 380 – This general-purpose alloy features excellent casting properties, making it easy to mold. Its advantageous mechanical properties make it suitable for various projects, such as enclosures for electronics, engine brackets, furniture frames, gearbox casings, and power tools.
- 390 – The aluminum alloy offers excellent vibration and wear resistance. Developed for die-casting car and truck engine blocks, it’s also suitable for manufacturing applications like producing valves and pump housings.
- 413 – This grade offers fantastic casting properties with excellent pressure tightness. It features in manufacturing projects for architectural components, hydraulic cylinders, and equipment in the dairy industry for milking cows, etc.
- 443 – This is the most adaptable aluminum alloy, making it suitable for producing consumer goods requiring plastic deformation after completing the casting process.
- 518 – The grade also offers excellent versatility in manufacturing projects. It has excellent corrosion resistance, making it suitable for aerospace and escalator components and ornamental hardware.
Popular Zinc Die Casting Alloys
Zinc alloys offer another versatile material popular in metal die-casting projects. Zinc is the most malleable and user-friendly alloy available and is suitable for hot chamber casting. Some of its unique properties include adaptability to a range of projects, excellent strength, and compatibility with plating projects.
Since it’s a highly castable material, it also offers excellent wear resistance, making it suitable for high-volume production and prototyping projects. Zinc is heavier than other options like magnesium and aluminum, and many manufacturers produce zinc alloys combined with magnesium, copper, and aluminum.
Here are the common grades of zinc alloys used in metal die-casting projects.
- Zamak 2 – This material features alloys with copper. It usually features in plastic injection molding tooling design and construction.
- Zamak 3 – This alloy is more general-purpose, making it suitable for various casting projects. It features exceptional dimensional stability and wear resistance, featuring in more than 60% of die-casting projects in North America. Some parts produced with this material include plumbing fittings and ceiling fans.
- Zamak 5 – This alloy has properties similar to Zamak 3, with improved tensile strength but less project adaptability. It’s common to see this material feature in wheel balancing weights and other automotive parts.
Popular Magnesium Die Casting Materials
Lighter than aluminum, magnesium offers another versatile die-casting material. It’s highly machinable and ideal for cutting intricate dies or completing high-quality surface finishes with CNC processes.
Magnesium suits hot-chamber casting processes and is more user-friendly and easier to work with than aluminum alloys—manufacturers often alloy magnesium with metals like zinc, aluminum, silicon, and manganese.
- AM60 – This alloy features excellent strength, castability, ductility, and vibration dampening. Manufacturers use the material to construct automotive components like panels and seat frames.
- AZ91D – Another general-purpose magnesium alloy offering exceptional castability, high strength-to-weight ratio, and excellent corrosion resistance. Some applications for this material include powertrain and mechanical components.
- AE42 & AS41B Rare earth alloys – These materials are expensive but are ideal for high-temperature applications, offering excellent corrosion resistance, creep resistance, and ductility. These alloys feature in automotive components.
In Closing – Other Popular Die Casting Materials
While aluminum, magnesium, and zinc are the most popular die-casting materials, manufacturers often rely on other popular metals like copper, lead, silicon tombac, and tin alloys.
- Zinc-aluminum alloys feature the ZA prefix for easy identification. ZA alloys with an aluminum content lower than 11% are suitable for hot chamber die-casting processes and
- Copper alloys feature excellent hardness, strength, corrosion resistance, and dimensional stability. Tin and lead alloys are very dense and resistant to corrosion.