One of the most popular metal casting methods is die casting. It is known for its versatility and the number of products it can produce. There’s a wide range of factors that allow this process to produce intricate product designs to fulfill advanced engineering requirements.
Now let’s take a look at the advantages and disadvantages of die casting, and the comparison of parts processed by other manufacturing methods.
What is Pressure Die Casting?
Pressure die casting is a quick, reliable, and cost-effective manufacturing process for producing high-volume, metal components with tight tolerances. The pressure die casting process consists of injecting molten metal alloy into a steel mold (tool) under high pressure. This molten material solidifies rapidly (from milliseconds to a few seconds) to form a net-shaped component. Upon curing, it is automatically extracted.
Depending on the amount of pressure used, the process has two types: low-pressure die casting and high-pressure die casting. The latter has wider application, about 50% of all light alloy casting production while the former comprises about 20% of the total production but currently, its applications are also increasing.
High-pressure die casting is ideal for castings that require tight tolerances and detailed geometry. Here, the extra pressure pushes the metal into more detailed features in the mold. Low-pressure die casting, on the other hand, is commonly applied to larger and non-critical parts.
Since the price of the machine and the dies are expensive, pressure die casting is viable only for high-volume production.
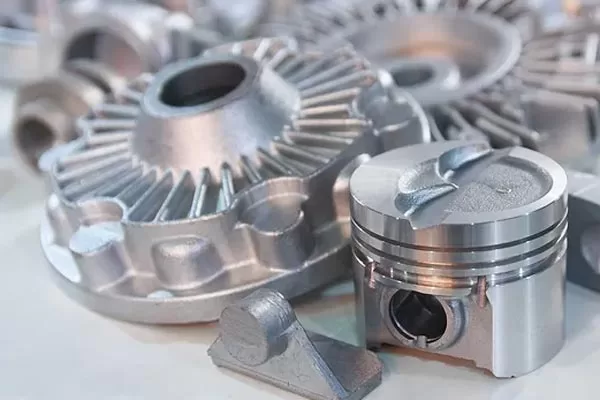
Pressure die casting parts
The Advantages of Pressure Die Casting
High Production Efficiency
The pressure die casting process is easy to operate and automate. Generally, the cold chamber die casting machine can accommodate die-casting 50 to 90 times per hour while the hot chamber die casting machine can do 400 to 900 times per hour.
Excellent Dimensional Accuracy and Smooth Cast Surfaces
The general tolerance of die-casted parts for aluminum can have an internal diameter within +/- 100 microns. With zinc, it is at half of the tolerance +/-50 or even at +/- 25. Due to the high dimensional accuracy and high surface finish of the process, less demanding die casting can be used directly, which avoids further machining, improving the use of the alloy and saving manufacturing costs.
High Mechanical Properties
Since the molten metal cools down quickly and crystallizes under pressure, a layer of crystalline grains forming near the surface of the die-casted part is compact and fine. This renders both strength and hardness to the part.
Complex Parts
Die casting can be used for designs with complex thin-walled parts. The wall thickness of the part can be smaller compared to sand casting and metal mold casting. It can create parts with a minimum wall thickness of 0.5mm. For zinc alloy die casting it can have 0.3mm.
Embedding of Other Materials
Complex inserts and fasteners can be included in the die casted parts. This can save on valuable material and production costs. You can achieve complex parts and improve their performance. It also reduces the assembly work.
Varied Surface Texture
Die casted parts can have many finishing surfaces and techniques. It can also achieve smooth or textured part surfaces.
Disadvantages of Pressure Die Casting
Porosity
In die casting, gas cavities are a common occurrence since the molten metal fills the mold cavity fast during the process. It also has no gas permeability. The presence of a gas cavity cannot be cured by heat treatment or even with high temperatures. To prevent this the machining allowance of parts should not be too large. Otherwise, the hardened layer on the surface will be removed to reveal the surface.
Not suitable for Small Batch Production
Since the die casting process is complicated and costly, it is not suitable for batch production. Therefore, it is not advisable for small-scale production as it is not economical.
Relatively Short Lifespan for the Molds
Some of the metals or alloys used in die casting have high melting points and can cause thermal fatigue on the molds. Today, the common materials used in die casting are aluminum alloys. Zinc alloys, magnesium alloys, and so on.
Significant Investment Requirement
The casting machines needed in the process and other related materials can be costly, compared to other casting processes. Thus, pressure die casting is more economical for large batch production.
Conclusion
In pressure die casting, the advantages outweigh its disadvantages, thus, it is now being used more as a manufacturing technique. Many everyday products are made from die casting like laptops, cameras, motorcycles, and automobiles.