Silicone molding has become a pivotal technique in producing wearable electronics, offering unique advantages that enhance functionality and comfort. This process allows for the creation of lightweight, flexible, and durable components that mold seamlessly to the contours of your body. As technology evolves, the wearable market’s demand for versatile and efficient manufacturing methods continues to rise.
Incorporating silicone into your designs can significantly improve the user experience, making devices more adaptable to everyday use. The material’s biocompatibility and resistance to environmental factors make it an ideal choice for health-tracking wearables, smartwatches, and fitness bands. With silicone molding, you can achieve high-quality products that perform well and look aesthetically pleasing.
Exploring silicone molding opens up opportunities for innovation and creativity in wearable electronics. You can leverage this technology to create customized solutions that cater to users’ individual needs, propelling your products ahead of the competition. The future of wearables is bright, and understanding the role of silicone molding is essential for staying at the forefront of this exciting industry.
Fundamentals of Silicone Molding
Silicone molding plays a crucial role in the production of wearable electronics. Understanding the material properties and processes enables you to achieve optimal design results.
Material Properties
Due to its unique properties, silicone is highly favored in wearable electronics. It is flexible, durable, and resistant to extreme temperatures, making silicone suitable for continuous use in diverse environments.
Silicon rubber is also biocompatible, making it ideal for skin contact applications. Additionally, its chemical resistance ensures longevity in devices that may encounter sweat or moisture.
Key properties include:
- Flexibility: Allows for comfortable wear.
- Durability: Resists wear and tear.
- Biocompatibility: Safe for skin contact.
These properties are essential when considering how silicone will perform in wearable applications.
Molding Processes
Silicone molding encompasses various techniques tailored to specific needs. Standard methods include injection molding and compression molding.
Injection molding involves forcing silicone into a mold under pressure. This method allows for intricate designs and rapid production cycles, and it is particularly effective for high-volume manufacturing.
Compression molding involves placing silicone into a mold and applying heat and pressure. This method is suited for more significant parts and can be more cost-effective for smaller batch productions.
Consider these factors when selecting a molding process:
- Complexity of Design: Intricate designs favor injection molding.
- Production Volume: High volumes favor injection molding for efficiency.
- Part Size: Compression molding may be better for larger items.
Understanding these processes will aid in choosing the proper method for your wearable electronics projects.
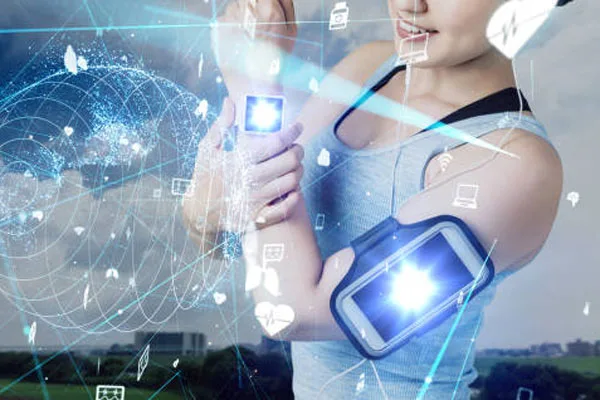
Silicone wearable sensors
Application in Wearable Electronics
- Health and Fitness Trackers: Silicone is commonly used in the production of bands and casings for fitness trackers and smartwatches, providing comfort and flexibility while being water and sweat resistant.
- Medical Devices: Wearable medical sensors and devices, such as glucose monitors and heart rate trackers, can benefit from silicone’s biocompatibility and softness, making prolonged wear more comfortable.
- Smart Clothing: Silicone molding can create conductive and non-conductive zones in smart fabrics that monitor physiological parameters (like temperature and heart rate) while offering comfort and breathability.
- Biosensors: Wearable biosensors for monitoring various health metrics can employ silicone molds to create flexible, skin-friendly interfaces that are capable of accurately capturing biological signals.
Design Considerations
In wearable electronics, design considerations for silicone molding involve flexibility, biomechanical compatibility, and user comfort. Silicone’s inherent flexibility enables it to conform to various body shapes and movements, enhancing user experience.
Factors to consider include:
- Material Thickness: Thinner molds can increase comfort and reduce bulk.
- Surface Texture: Smooth finishes can improve wearability, while textured surfaces enhance grip.
- Color and Aesthetics: Customizable colors and finishes help match personal styles.
These aspects are critical to ensure that the final product is functional and appealing to users.
Manufacturing Techniques
Manufacturing techniques for silicone molding in wearable electronics include injection molding, compression molding, and liquid silicone rubber (LSR) processes.
- Injection Molding: Offers high precision and repeatability, making it suitable for large production runs.
- Compression Molding is ideal for creating more significant parts with complex shapes.
- Liquid Silicone Rubber: Enhances the ability to produce intricate designs and provides superior thermal stability.
These methods determine the quality, durability, and overall performance of the components used in your devices.
Integration with Electronic Components
Integrating silicone-molded parts with electronic components requires careful planning. The silicone must accommodate sensors, batteries, and other hardware without compromising functionality.
Key integration aspects include:
- Encapsulation: Silicone can protect sensitive electronics from moisture and dust.
- Bonding Techniques: Adhesives or mechanical interlocks can securely attach silicone to electronic components.
- Compatibility with Electronics: Ensuring materials used, such as signal transmission, do not interfere with device functionality.
Considering these factors, your wearable electronics can achieve better performance and longevity.
For professional assistance with silicone molding for wearable electronics, consider contacting Nicerapid.com to get a quote and fulfill your manufacturing needs.