Silicone molding stands as a versatile and indispensable technique in various industries, offering a gateway to precision and efficiency. This blog is dedicated to showcasing the real-world success stories of businesses that have harnessed silicone molding to their advantage.
In the forthcoming sections, we will delve into case studies from the automotive, medical device manufacturing, consumer electronics, art and design, as well as aerospace and defense sectors. Each case study will unveil how silicone molding has empowered these industries, not only in terms of cost and time savings but also in elevating product quality and functionality. Let’s explore the transformative power of silicone molding.
Case Study 1: Automotive Industry – SpeedCraft Automotive
SpeedCraft Automotive, a leader in the automotive industry, has been at the forefront of precision engineering. Their utilization of silicone molding has been pivotal in optimizing the manufacturing process, resulting in significant cost and time savings, and elevating the production of complex components to a level of unparalleled excellence.
One of the key benefits of silicone molding is its versatility. Silicone molds can be used to create a wide range of components, from simple gaskets and seals to complex aerodynamic parts. This makes silicone molding an ideal solution for SpeedCraft Automotive, which manufactures a diverse range of automotive components.
Another key benefit of silicone molding is its accuracy. Silicone molds can be produced to extremely tight tolerances, ensuring that the components produced are of the highest quality. This is essential for SpeedCraft Automotive, which produces components for high-performance vehicles.
Silicone molding has also enabled SpeedCraft Automotive to streamline its manufacturing process. By using silicone molds, SpeedCraft Automotive can produce multiple components simultaneously, reducing production time and costs. Additionally, silicone molds are reusable, which further reduces manufacturing costs.
The overall impact of silicone molding on SpeedCraft Automotive has been significant. By utilizing silicone molding, SpeedCraft Automotive has been able to achieve the following:
- Reduce manufacturing costs
- Reduce production time
- Improve the quality of components
- Streamline the manufacturing process
- Gain a competitive edge
SpeedCraft Automotive is just one example of how silicone molding can be used to optimize the manufacturing process in the automotive industry. Silicone molding is a versatile, accurate, and cost-effective solution for the production of a wide range of automotive components.
Case Study 2: Medical Device Manufacturing – MedTech Innovations
MedTech Innovations is a renowned player in the medical device manufacturing sector, where precision and safety are non-negotiable. The company’s journey with silicone molding serves as a testament to its effectiveness. This case study will delve into the regulatory intricacies and material compatibility considerations in the medical field. It will emphasize how MedTech Innovations has harnessed silicone molding to not only meet but exceed regulatory standards, thereby ensuring enhanced product quality and, most importantly, patient safety.
Regulatory Intricacies
The medical device industry is heavily regulated, with strict compliance requirements in place to ensure the safety and efficacy of products. Silicone molding is an increasingly popular manufacturing process for medical devices, but it is important to note that it is subject to the same regulatory scrutiny as other manufacturing processes.
One of the key regulatory considerations for silicone molding is the use of materials that are biocompatible and safe for implantation or use in the body. Silicone materials are generally biocompatible, but it is important to select the right grade of silicone for the specific application. MedTech Innovations works closely with its suppliers to ensure that the silicone materials it uses meet all applicable regulatory requirements.
Another key regulatory consideration for silicone molding is the manufacturing process itself. MedTech Innovations has a robust quality management system in place to ensure that its silicone molding processes are compliant with all applicable regulations. This includes regular inspections and audits of its manufacturing facilities and processes.
Material Compatibility Considerations
In addition to regulatory compliance, it is also important to consider material compatibility when using silicone molding for medical devices. Silicone is a versatile material that is compatible with a wide range of other materials. Still, it is important to test the compatibility of the silicone material with any other materials that it will come into contact with during use.
MedTech Innovations conducts extensive material compatibility testing to ensure that its silicone-molded medical devices are safe and effective. This testing includes evaluating the compatibility of the silicone material with other materials such as blood, tissue, and fluids.
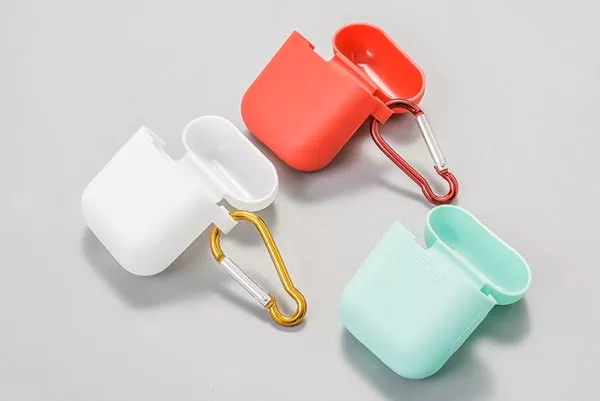
High quality silicone headphone case
How MedTech Innovations Harnesses Silicone Molding
MedTech Innovations harnesses silicone molding to manufacture a wide range of medical devices, including implants, prosthetics, and diagnostic tools. The company’s expertise in silicone molding allows it to produce high-quality, precision components that meet all applicable regulatory standards.
One of the key advantages of silicone molding for medical devices is that it allows for the creation of complex shapes and geometries. This is essential for many medical devices, such as implants and prosthetics, which need to conform to the human body. Additionally, silicone molding can produce components with very tight tolerances, which is important for many medical devices.
MedTech Innovations also uses silicone molding to produce medical devices with a variety of surface finishes. This includes smooth, textured, and non-stick surfaces. The ability to create a variety of surface finishes is important for many medical devices, as it can affect factors such as biocompatibility, performance, and cleaning.
Case Study 3: Consumer Electronics – TechGizmo Inc.
TechGizmo Inc., a leading name in the consumer electronics industry, has carved a niche for itself by pushing the boundaries of innovation. The company’s utilization of silicone molding has been pivotal in achieving a seamless synergy between aesthetics and functionality.
Silicone molding is a versatile manufacturing process that allows for the creation of complex shapes and geometries with high precision. This makes it an ideal solution for TechGizmo Inc., which produces a wide range of consumer electronics products with intricate designs.
One of the key benefits of silicone molding is its ability to create components with a smooth, seamless finish. This is essential for TechGizmo Inc., which produces products that are known for their sleek and stylish designs. For example, TechGizmo Inc. uses silicone molding to produce the casing for its flagship smartphone, the TechGizmo X10. The silicone mold ensures that the casing is perfectly smooth and free of any imperfections, giving the phone a premium look and feel.
In addition to its aesthetic benefits, silicone molding also enhances the functionality of TechGizmo Inc.’s products. For example, the company uses silicone molding to produce the gaskets and seals for its wearables. Silicone is a highly durable and water-resistant material, making it ideal for creating seals that protect the delicate internal components of wearables from sweat and moisture.
Another key benefit of silicone molding is its flexibility. Silicone molds can be easily modified, making them ideal for prototyping iterations. This is important for TechGizmo Inc., which is constantly innovating and developing new products. For example, the company uses silicone molding to prototype the cases for its new smartphones. This allows TechGizmo Inc. to quickly test different designs and make necessary modifications before launching a new product.
Overall, silicone molding has played a pivotal role in TechGizmo Inc.’s success. By leveraging the benefits of silicone molding, TechGizmo Inc. has been able to produce consumer electronics products that are both aesthetically pleasing and highly functional.
Conclusion
The case studies we’ve explored underscore the remarkable adaptability and utility of silicone molding across a diverse array of industries. These stories serve as a testament to its transformative power, not only in terms of cost and time savings but also in elevating product quality and functionality. As we look to the future, the potential of silicone molding in various industries remains boundless. We encourage businesses to explore how silicone molding can serve their specific needs, and we anticipate that its role in shaping industries will only continue to expand.
For businesses seeking to leverage the benefits of silicone molding, consider partnering with experts in the field, like Nice Rapid, a manufacturing company specializing in silicone molding. Their expertise can be the key to your success. Explore the possibilities today!