Silicone molding is a versatile and accessible method for creating duplicate objects and prototypes with precision and ease. Whether you’re a hobbyist, an artist, or a product designer, silicone molding can help you replicate intricate details, experiment with various materials, and bring your ideas to life. In this comprehensive guide, we will take you through the basics of silicone molding, from materials and techniques to the step-by-step process of creating your molds and castings.
Silicone Rubber: A Versatile Material for Professional Applications
Silicone rubber is a synthetic elastomer with a wide range of properties that make it ideal for a variety of professional applications. It is non-toxic, heat-resistant, flexible, and durable, making it a popular choice for industries such as automotive, aerospace, medical, and electronics.
There are two main types of silicone rubber: tin-cure and platinum-cure. Tin-cure silicone rubber is the more common type and is less expensive than platinum-cure. It is also more flexible and easier to work with. However, tin-cure silicone rubber has a shorter shelf life and can release harmful fumes when curing.
Platinum-cure silicone rubber is more durable and heat-resistant than tin-cure silicone rubber. It is also non-toxic and has a longer shelf life. However, platinum-cure silicone rubber is more expensive and can be more difficult to work with.
When choosing a silicone rubber for a professional application, it is important to consider the following factors:
- Operating temperature: Silicone rubber can withstand a wide range of temperatures, but it is important to choose a type that is rated for the operating temperature of the application.
- Chemical resistance: Silicone rubber is resistant to many chemicals, but it is important to choose a type that is resistant to the specific chemicals that will be encountered in the application.
- Physical properties: Silicone rubber can be formulated to have a variety of physical properties, such as hardness, elasticity, and tear strength. It is important to choose a type that has the desired physical properties for the application.
Once the appropriate type of silicone rubber has been chosen, it is important to follow the manufacturer’s instructions carefully to ensure proper curing. Curing is the process by which the silicone rubber becomes cross-linked and develops its desired properties.
Silicone rubber is a versatile material that can be used for a variety of professional applications. By choosing the right type of silicone rubber and following the manufacturer’s instructions, engineers and technicians can create products and components that are durable, reliable, and safe.
Here are some examples of professional applications for silicone rubber:
Automotive: Silicone rubber is used in a variety of automotive applications, such as gaskets, seals, hoses, and belts. It is also used to make electrical insulation and other components.
Aerospace: Silicone rubber is used in a variety of aerospace applications, such as seals, gaskets, and fuel lines. It is also used to make components for aircraft engines and other systems.
Medical: Silicone rubber is used in a variety of medical applications, such as implants, prosthetics, and surgical instruments. It is also used to make medical tubing and other components.
Electronics: Silicone rubber is used in a variety of electronics applications, such as seals, gaskets, and encapsulation materials. It is also used to make electrical insulation and other components.
Silicone rubber is a valuable material for a wide range of professional applications. By understanding its properties and choosing the right type, engineers and technicians can create products and components that are durable, reliable, and safe.
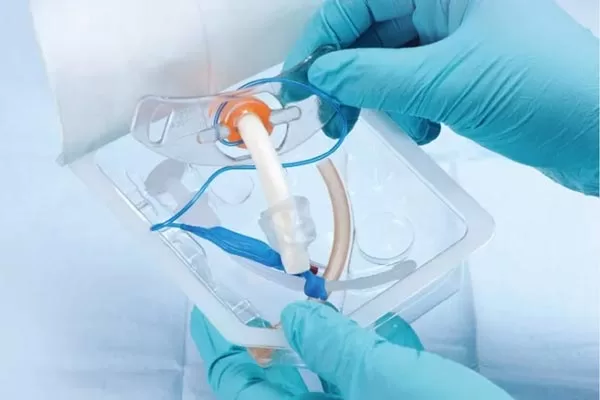
Medical device silicone tubing
Materials and Tools for Silicone Rubber Molding
Silicone rubber molding is a versatile process that can be used to create molds for a variety of casting materials, such as resin, wax, plaster, and concrete. The process is relatively simple and can be done at home with a few basic materials and tools.
Here is a list of the essential materials and tools you will need for silicone rubber molding:
Materials:
- Silicone rubber
- Release agent
- Modeling clay or objects to be molded
- Casting material (resin, wax, plaster, etc.)
Tools:
- Mixing containers
- Stirring sticks
- Digital scale
- Mold box
- Utility knife
- Vacuum chamber (optional)
Silicone rubber: There are two main types of silicone rubber used for molding: tin-cure and platinum-cure. Tin-cure silicone rubber is less expensive and easier to work with, but it has a shorter shelf life and can release harmful fumes when curing. Platinum-cure silicone rubber is more durable, heat-resistant, and non-toxic, but it is more expensive and can be more difficult to work with.
Release agent: A release agent is used to prevent the silicone rubber from sticking to the mold. There are a variety of release agents available, such as mold release spray and wax.
Modeling clay or objects to be molded: The object you want to mold will be used to create a negative impression in the silicone rubber. This impression will then be used to cast the desired object.
Casting material: The casting material is the material that will be used to create the final object. Popular casting materials include resin, wax, plaster, and concrete.
Mixing containers: You will need two mixing containers to mix the silicone rubber and the release agent.
Stirring sticks: Stirring sticks are used to mix the silicone rubber and the release agent.
Digital scale: A digital scale is used to measure the silicone rubber and the release agent.
Mold box: A mold box is used to contain the silicone rubber while it is curing. Mold boxes can be made from a variety of materials, such as wood, metal, and plastic.
Utility knife: A utility knife is used to trim the silicone rubber mold once it is cured.
Vacuum chamber: A vacuum chamber is an optional tool that can be used to remove air bubbles from the silicone rubber.
Creating the Mold
To create a silicone rubber mold, follow these steps:
- Prepare the model: Clean and seal the object to be molded and attach it to a baseboard.
- Make the mold box: Construct a mold box around the model, ensuring a tight seal.
- Mix and pour silicone: Measure and mix the silicone rubber components according to the manufacturer’s instructions, and pour the silicone rubber into the mold box, starting at the corners and working your way in.
- Cure the silicone: Allow the silicone rubber to cure for the recommended time, typically 24-48 hours.
Once the silicone rubber has cured, you can remove the mold from the mold box. Your silicone rubber mold is now ready to use!
Demolding and Cleanup
Once the silicone rubber has cured, it is time to remove the mold from the mold box and prepare it for casting.
Demolding
To de-mold the silicone rubber mold, carefully remove the mold box and release the mold from the model. Be careful not to damage the mold, especially if it is delicate or has thin or intricate features.
Trimming and Cutting
Once the mold is demolded, you may need to trim excess silicone and create a seam line. To trim excess silicone, use a sharp utility knife to cut away any extra material. To create a seam line, use the utility knife to cut a shallow groove around the perimeter of the mold. This will help to prevent the casting material from leaking out when you pour it into the mold.
Once the mold has been trimmed and cleaned, it is ready to use for casting.
Here are some additional tips for demolding and cleaning silicone rubber molds:
- If the mold is difficult to de-mold, try using a gentle release agent, such as mold release spray or wax.
- Be careful not to over-trim the mold, as this can damage the mold and make it difficult to use.
- If you are creating a mold with multiple parts, be sure to mark the alignment points before demolding. This will help you to reassemble the mold correctly when you are ready to cast.
- To clean the mold, use a mild soap and water solution. You can also use a soft brush to remove any stubborn casting material.
- Once the mold is clean, dry it thoroughly before using it again.
By following these tips, you can ensure that your silicone rubber molds are demolded and cleaned properly so that you can use them to create high-quality castings.
Casting
Once you have created a silicone rubber mold, you can use it to cast replicas of your original object.
Preparing the Casting Material
The first step is to mix and prepare the casting material. Follow the manufacturer’s instructions carefully, as the mixing and curing process can vary depending on the type of casting material you are using.
Pouring the Casting Material
Once the casting material is prepared, carefully pour it into the silicone rubber mold. Be careful not to overfill the mold, as this can cause the casting material to leak out. You may want to use a funnel to help control the flow of the casting material.
Curing the Casting Material
Once the mold is filled, allow the casting material to cure according to the manufacturer’s instructions. The curing time can vary depending on the type of casting material you are using.
Once the casting material has cured, you can remove it from the silicone rubber mold. Your casting is now complete!
Here are some additional tips for casting with silicone rubber molds:
- Make sure that the mold is clean and dry before casting.
- If you are casting a complex object, use a vacuum chamber to remove air bubbles from the casting material.
- To create a smooth finish on your casting, you can use a release agent before pouring the casting material.
- Be careful not to over-de-mold the casting, as this can damage it.
By following these tips, you can ensure that your castings are high-quality and durable.
Here are some examples of casting materials that you can use with silicone rubber molds:
- Resin
- Wax
- Plaster
- Concrete
- Soap
- Chocolate
Silicone rubber molds are versatile and can be used to create a variety of objects, from simple shapes to complex sculptures. With a little practice, you can use silicone rubber molds to create beautiful and unique pieces.
Troubleshooting and Tips
Air Bubbles
One of the most common problems encountered in silicone rubber molding is air bubbles. Air bubbles can occur for a variety of reasons, such as pouring the silicone rubber too quickly, not mixing the silicone rubber thoroughly, or not using a vacuum chamber.
To prevent air bubbles, try the following tips:
- Pour the silicone rubber slowly and carefully.
- Mix the silicone rubber thoroughly until there are no streaks.
- Use a vacuum chamber to remove air bubbles from the silicone rubber.
If you do get air bubbles in your silicone rubber mold, you can try to remove them by using a toothpick or a needle to pop the bubbles. You can also use a heat gun or a blowtorch to gently heat the mold, which will help to expand the air bubbles and make them easier to remove.
Undercuts
Undercuts are areas of the model that have overhangs or recesses. Undercuts can make it difficult to remove the model from the silicone rubber mold without damaging the mold.
To prevent undercuts, try to design your model without them. If you cannot avoid undercuts, you can use a mold release agent to help prevent the silicone rubber from sticking to the model. You can also try using a mold-release spray or wax.
Mold Release Issues
If you are having trouble removing the silicone rubber mold from the model, it is possible that the mold release agent was not applied properly.
To ensure that the mold release agent is applied properly, try the following tips:
- Clean the model thoroughly before applying the mold release agent.
- Apply a thin, even coat of mold release agent to the entire surface of the model.
- Allow the mold release agent to dry completely before pouring the silicone rubber.
If you are still having trouble removing the silicone rubber mold from the model, you can try using a gentle release agent, such as mold release spray or wax. You can also use a heat gun or a blowtorch to gently heat the mold, which will soften the silicone rubber and make it easier to remove.
Safety Precautions
Safety is paramount when working with silicone and casting materials. Here is an overview of essential safety precautions to follow:
- Wear gloves and eye protection: Silicone rubber and casting materials can irritate your skin and eyes, so it is important to wear gloves and eye protection when working with them.
- Work in a well-ventilated area: Some of the fumes released by silicone rubber and casting materials can be harmful, so it is important to work in a well-ventilated area.
- Avoid contact with skin: If you do get silicone rubber or casting material on your skin, wash it off immediately with soap and water.
- Follow the manufacturer’s instructions: Be sure to follow the manufacturer’s instructions carefully when using silicone rubber and casting materials.
Here are some additional safety tips to keep in mind:
- Be careful not to overheat silicone rubber, as this can release harmful fumes.
- If you are using a vacuum chamber, make sure that it is properly vented to prevent the buildup of flammable fumes.
- Be aware of the fire hazard associated with some casting materials, such as resin and alcohol.
- Keep silicone rubber and casting materials out of the reach of children and pets.
By following these safety precautions, you can minimize the risk of accidents and injuries when working with silicone rubber and casting materials.
Conclusion
In this guide, we’ve covered the fundamental aspects of silicone molding for beginners, from selecting the right silicone rubber to creating molds and casting objects. With practice and patience, you can master this versatile technique and bring your creative ideas to life. Enjoy your journey into the world of silicone molding!
For large-scale silicone molding needs, you can contact Nice Rapid. They are the experts in the silicone molding process.