Vacuum casting has surpassed the prototyping market by becoming a commonly used method in all phases of production to accommodate several design alterations. This casting procedure may provide a completely new prototype in less than 30 days for complex designs.
One of the most impressive things about vacuum casting is it requires less energy than CNC machining or injection molding, resulting in cheaper energy consumption expenses.
This method is intended to improve any production process by reducing delivery times. The technique’s success is excellent, with approximately 90% of all industries throughout the world employing vacuum casting to create prototypes and manufacture high-quality parts and products.
Even small business operations can benefit from this technology for them to lower their production costs; however, the first step that the entrepreneur must take is to become familiar with all steps of the vacuum manufacturing process.
The development of die casting, the handling of runners and overflows, the handling of surface treatments, and even aspects linked to the packaging and distribution of these materials all require a thorough understanding of the main casting process. We’ll go over a few key points about each step of the process that can help you save money.
Die Casting Cost Reduction
The first phase is for the design team to do an in-depth analysis of the product’s features, but developers can also make the process more economical by obtaining a specific design using low-cost materials on short deadlines in order to make adjustments to the final cast of the product. You will save money and make greater use of the casting process by getting a precise mold, which will reduce the cost and wear on your production line.
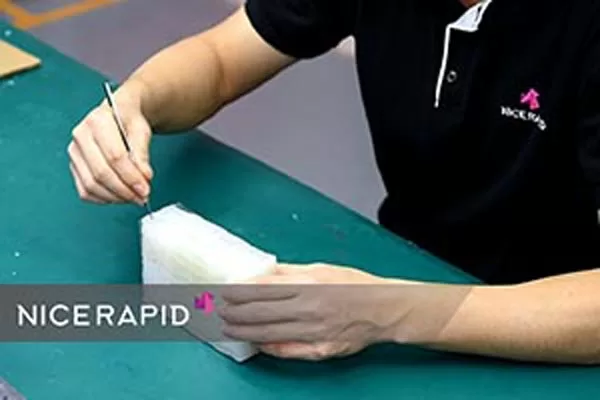
Opening mould
Eliminating Runners and Overflows Saves Money
To save time and money, two distinct but interconnected procedures must be handled at this point. The first is pertains with the cooling of the product after it has been made using the mold. This can be managed by using alternate chemical products that can speed up the process. This expense incurred will be offset by greater output or production.
The second step relates to the collection, recycling, and re-use of scraps produced during the production process. Choosing the best method is closely linked to the sort of product we are dealing with, having control over this process will allow you to manage the production budget and stick within its limits.
Saving Money on Surface Treatments
The finished appearance/look of a product can be accomplished by timely methods and techniques that provide good results in the same way that extensive comprehensive modifications do. Even dealing with a difficult client who wants specific conditions, you can use operations like degassing, sandblasting, and neatening because they typically offer some of the best results to finished products while being less time-consuming than other manual techniques.
Saving Money on Packaging and Delivery
While we cannot say that expediting this stage is good for your business, it can be done without compromising the end product’s quality. Let us take a moment to realize that how we supply our goods will have a significant impact on our customer.
With that in mind, the best approach to accomplish this at a low cost and on schedule is to handle all aspects of logistics while keeping a careful eye on the materials used in packaging, how it will be stored, and the shipping service that will be used to deliver the finished product.
Overall, vacuum casting provides several advantages for all your production needs and applications, but this technique is most useful when a large number of high-quality prototypes are required.
Product development teams that want to build pre-launch prototypes for customer trials, marketing models, or functional prototypes can benefit from vacuum casting. The technology is also appropriate for small-batch manufacturing of end-use components due to its high production quality.
If you are still unsure whether it is the correct choice for your rapid prototyping needs, please contact us at Nice Rapid.