Ever marveled at the sleek metal components in your car or smartphone? Chances are, pressure die casting helped bring them to life! When manufacturers need complex metal parts with jaw-dropping accuracy and mirror-like surface finishes, pressure die casting is the go-to method. This fascinating process has evolved dramatically over decades, offering a reliable way to create stunning metal components that would make even a master sculptor jealous. Let’s peek behind the manufacturing curtain to see if pressure die casting might be the perfect match for your next project!
Metal Under Pressure: The Magic Behind Perfect Parts
At its heart, pressure die casting is beautifully straightforward—though don’t tell that to the engineers who’ve spent years mastering it! Imagine putting molten metal into a steel mold under pressure that makes deep-sea creatures uncomfortable. This extreme pressure is the secret sauce that makes pressure die casting special, forcing liquid. Liquid every fillsd cranny of the mold, capturing details finer than a human hair.
Once the metal cools from “lava-hot” to “solid-as-a-rock,” the die opens like a treasure chest, revealing the perfectly formed part inside. This makes pressure die casting the champion of manufacturing processes when you need parts with paper-thin walls, intricate shapes that look impossible to make, and dimensions precise enough to satisfy even the pickiest quality inspector.
The pressure die casting family has two main branches: hot and cold chamber processes. Think of them as siblings with different personalities! Hot chamber pressure die casting is like the speedy, impatient sibling—perfect for easily melting zinc and other metals. Cold chamber pressure die casting is the more versatile, strong-willed sibling, handling aluminum, magnesium, and copper alloys that would burn through hot chamber equipment.
Choosing Your Metal: The Alloy Adventure
The success of your pressure die casting project hinges on picking the perfect metal for the job—it’s like choosing the right ingredient for a gourmet recipe. Aluminum alloys are the superstars of the pressure die casting world, offering an impressive combo package: They flow into molds like water, weigh less than your morning coffee, and provide strength that belies their lightweight nature.
Zinc alloys shine in pressure die casting applications where you need that substantial, premium feel in your hand (think high-end electronics or decorative hardware) and surface finishes smooth enough to see your reflection. For the ultimate in lightweight performance, magnesium alloys are the featherweight champions of pressure die casting, delivering strength-to-weight ratios that make aerospace engineers giddy with excitement.
Each material brings its personality to the pressure die casting dance, affecting how quickly parts can be made, how long expensive molds will last, and how finished parts will perform in the real world. Choosing wisely can mean the difference between components that disappoint and ones that delight.
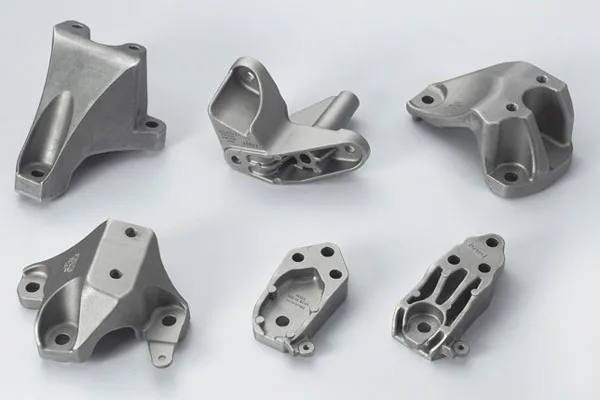
Aluminum Die casting for engine parts
The Tech Revolution: Smart Machines Make Better Parts
Modern pressure die casting has ridden the wave of technological advancement like a pro surfer, transforming from an art form dependent on operator skill to a high-tech process with computer precision. Today’s pressure die casting machines are like spacecraft of the manufacturing world—packed with sophisticated hydraulic systems that apply pressure with exquisite control, temperature monitors more precise than your home oven, and computer brains that ensure every cycle produces perfect parts.
One of the game-changing innovations in pressure die casting involves adding vacuum assistance—think of it as giving your process a superpower upgrade. By sucking air out of the mold before the metal rushes in, vacuum-assisted pressure die casting reduces pesky porosity issues and improves structural integrity. This technology has opened doors for pressure die casting to crash the party in new sectors, including automotive structural components, where strength isn’t just desirable—it’s a matter of safety.
Quality Challenges: Battling the Villains of Die Casting
Despite its impressive resume, pressure die casting isn’t without challenges—every manufacturing hero has villains to overcome! Porosity—those tiny air pockets that can hide inside your parts—is perhaps the most notorious troublemaker in pressure die casting. These microscopic bubbles form when gases get trapped during the high-pressure metal injection, potentially compromising your finished components’ stunning looks and mechanical strength.
Other potential defects in the pressure die casting rogues’ gallery include cold shuts (where flowing metal fronts meet but don’t correctly bond—like awkward handshakes at a networking event) and die soldering (where the metal sticks to the mold surface like overcooked pancakes to a pan). Fortunately, implementing proper process controls and clever die design principles helps minimize these issues in pressure die casting operations, ensuring your parts come out looking and performing their best.
Your Die-Casting Dreams, Our Engineering Reality
With our deep engineering expertise in pressure die casting, rapid prototyping, and low-volume manufacturing, we transform your most challenging metal component ideas into reality. We don’t just follow your specifications—we enhance them through our comprehensive Design For Manufacture approach, which optimizes every aspect of the pressure die casting process.
Our team’s extensive knowledge ensures your pressure die casting projects deliver maximum value without breaking your budget. We’ve spent years mastering the fine art of die design and process parameter optimization, helping eliminate those frustrating defects while maximizing part quality and production efficiency.
Whether you need lightweight automotive components, structurally critical aerospace parts, or consumer electronics with that premium look and feel, our pressure die casting expertise delivers results that exceed your expectations. Contact us today for a consultation and discover how our engineering-focused approach to pressure die casting can transform your manufacturing challenges into your most significant competitive advantage!