Have you ever thought about how car parts are made? When you need a part, you probably head to the nearest auto body shop and purchase whatever you need. Did you know that many of these parts are made using a hydraulic press?
In case you don’t know yet, this machine is part of the compression molding process, and there is a wide variety of this equipment to choose from in manufacturing a part.
It is necessary to know how these car parts are made through compression molding. In this article, we will take an in depth look at this process and the advantages it can offer.
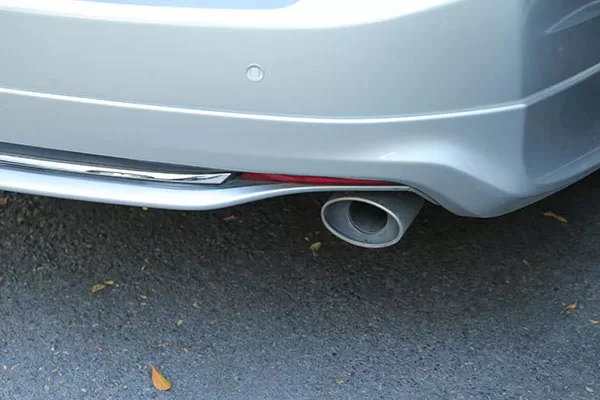
Compression molding in automotive industry
What is Compression Molding?
Compression molding is a good option for manufacturing large parts. It is an efficient technique in these types of requirements because there is only a small amount of material lost. Aside from efficiency, it also exhibits a straightforward process. This makes compression molding cost-effective and highly favoured by the automotive industry.
As mentioned, compression molding is a versatile and simple process using an open and heated mold cavity. It uses a thermoset composite material that is compressed to cover every space in the mold. This allows for manufacturing a wide range of parts with unique thicknesses, details, and lengths.
In compression molding, the end-product is unusually strong but has added benefits of resistance to corrosion and lightness with the use of sophisticated base materials.
You can summarize the compression molding process in these four easy steps:
Step 1. Tooling. One important factor in creating a perfect product is the right and strong metal tool that possesses the right shape and dimensions. This tool is placed in the press and heated to setup for molding.
Step 2. Heating the Material. Once the mold is ready, the material is poured into the mold and takes its shape.
Step 3. Compressing. The next step is compressing the material into the heated mold with the use of pressure.
Step 4. Removing from the Mold. When the pressure is released, the part is now ready to be removed from the mold.
Compression Molding for Car Parts
Although the compression molding process may seem easy, there are specific requirements that must be fulfilled. For example, the temperature of the mold should be between 250 and 400 degrees Fahrenheit. This temperature is determined by the type of materials and the design of the parts.
The whole process can be completed in as little as one minute or five minutes depending on the amount of heat and pressure necessary. This is what makes compression molding perfect for automobile manufacturers. It has a short curing time. Meaning, when you use this technique, you are guaranteed a high turnaround for products.
Some auto parts produced by compression molding include housing for airbags, headrests, crossbeams, floor parts, and seatbacks. If you look at current car models, you will find a wide range of parts that are composites from compression molding.
Due to its strength, rapid turnaround, and lightness, we will see more applications of compression molding in the future.