Have you ever wondered how brands make the grip parts on toothbrushes or plastic cooking spatulas? Molded objects can receive a second resin layer in the TPU injection molding process, aka “overmolding.” The result is a product with a combination of materials and user benefits.
A popular use of overmolding is to use a layer of soft, useful, and hand-friendly TPE – a rubber-like injection material molded over a rigid base layer.
Another strategy is to overmolded material of different finishes or colors to an item to improve or alter its cosmetics look. Overmolding has thousands of industrial applications in product manufacturing, from surgical equipment to toothbrushes.
What are the Benefits of Overmolding in Product Design?
- Mold soft-touch exteriors.
- Enhance feel and grip.
- Increase visual aesthetic to appeal to consumers.
- Reduce shock and vibration.
- Dampen sound.
- Provide an electrical insulator.
- Weatherproofing materials.
- Enhancing UV and chemical resistance.
- Extend product longevity.
5 Overmolding Applications in Our Life
Where do you encounter overmolded products in your everyday life? Here are five examples of overmolded products you might use every day.
1 DIY & Professional Tools
If you’re a contractor or professional artisan, you probably own a hammer with an ergonomically shaped plastic handle featuring a rubber grip. That’s an example of overmolding and its benefits with shock and vibration dampening.
Overmolding also features in hardware product design, from power tool casings to wrenches, pliers, tape measures, and many other DIY and professional tools. Overmolding of tooling components improves user operation and comfort while preventing injury.
2 Household Products
There are dozens of overmolded products around your home that you’ve never thought of before. Overmolded products offer chemical and bacterial resistance in applications around the bathroom and kitchen and style and ergonomics in products you use in the lounge and bedroom.
Some common examples of overmolded products in the bathroom include toothbrushes, toilet brush handles, shower brush handles, plunger handles, shower mats, bath drawers, and many more. Overmolding in household item design features in fan casings, multi-port chargers, reusable food containers, and more.
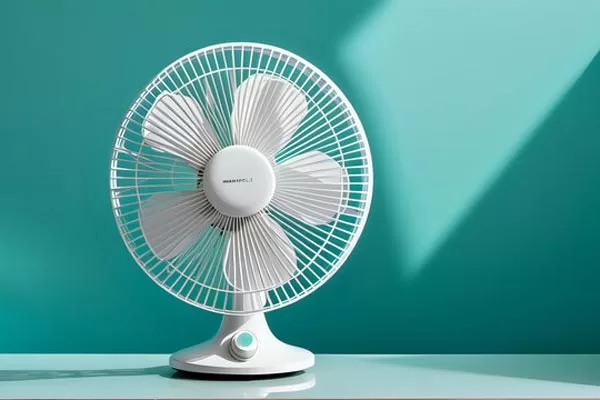
Fan blade
3 Kitchenware & Cookware
Plastics must be food safe and uncontaminated by the production process. Plastic injection molding is ideal for high-volume production that meets regulatory guidelines on food safety requirements. Overmolding features in a variety of cookware and kitchenware.
From handles on pots, pans, and lids to spatula handles, pot covers, cutting boards, scissors, and more, overmolding is a useful manufacturing method for brands.
4 Surgical & Medical Products
The medical sector values product safety and precise manufacturing in product prototyping and mass production. Medical professionals and patients must only come in contact with medical and surgical materials in any products used in medical settings.
Syringes, lab consumables, patient monitors, dilators, needles, and catheters are a few examples of medical and surgical equipment produced through overmolding processes.
5 Car Interiors & Trim
Your car relies on overmolding for many interior and exterior components. Car bumpers, wheel wells, engine covers, fenders, and spoilers are all examples of external car components made using overmolding practices.
Overmolding also features in interior component design, with many people in the industry referring to them as car moldings. From the dashboard and steering wheel, to pedal covers, gearshifts, air vents, door trim, edge trim, and seat trim, overmolding has many applications in interior component manufacturing.
Car trim has practical advantages. It assists with lowering the vehicle’s weight, despite enhancing the visual aesthetic of the car’s interior design. When ordering their vehicles from the factory, manufacturers can offer customers trim in various finishes and colors.
Car molding can feature combination materials, such as aluminum, chrome, or other types of plating, using an ” insert molding process.”