If you are familiar with the plastic injection molding process, you might have encountered some of the materials the process used. Their names seem straight out of a chemistry class and very hard to remember.
No matter how hard it is to know their names, you need to be familiar with them because it will impact the plastic injection molding process.
Fortunately, you don’t have to go back to your chemistry class to choose the right material. There are other factors that would influence your choice but before you get into them, you need to know the names and abbreviations of the most popular material used in plastic injection molding.
Acrylic (PMMA)
Poly(methyl methacrylate), PMMA or better known as Acrylic is strong, clear plastic. It is lightweight and a shatter-resistant substitute for glass. Since PMM is transparent, it has better optical clarity, allowing much light to pass through.
The most common acrylic, which is the least expensive, is frequently used in commodity products while the sun-grade options are more for outdoor signages.
Acrylonitrile Butadiene Styrene (ABS)
This is an engineering-grade thermoplastic that has a low melting point, which makes it easy to mold. ABS is available in different textures and finishes and can effectively absorb colorants. They are also known for their impact resistance and strength.
Nylon Polyamide (PA)
Polyamides (PA) encompasses a large group of raw materials for plastic injection and it can be either synthetic or natural. Nylon, a commonly used polyamide, is synthetic. The only drawback with using nylon is it can shrink and be difficult to fill a mold.
Polycarbonate (PC)
Most products made from polycarbonate are strong, durable, and impact resistant. This material is naturally transparent and shares some common properties with PMMA only it maintains its physical properties when exposed to high temperatures. When colored, polycarbonate can retain its color and strength.
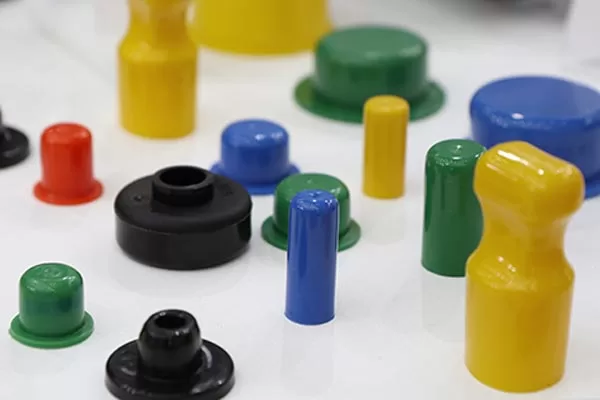
Plastic parts
Polyethylene (PE)
The majority of the plastic parts and products you see around you are made from polyethylene. There are three types of PE: high density(HDPE, PEHD), low density (LDPE), polyethylene terephthalate (PET, PETE).
This classification is based on its density which for plastic injection materials is a measurement that controls its other properties. Two of its types: HDPE and LDPE share a common property – resistance to chemicals. However, they differ in respective hardness, melting point, flexibility, and transparency.
Polyoxymethylene (POM)
Polyoxymethylene (POM) is a type of engineering plastic that is commonly known as acetal. It can be used in plastic injection molding. It is perfect for parts that require high stiffness, low friction, and excellent stability. Since this material has a crystalline structure, the parts are naturally white and opaque.
Polypropylene (PP)
Polypropylene shares similar characteristics with polyethylene (PE) with only a slight difference in heat resistance and hardness. Hence, it ranks second when it comes to the most used material for plastic injection molding.
Polystyrene (PS)
There are two types of polystyrene (PS) that are commonly used in injected parts: general-purpose polystyrene (GPPS) and high impact polystyrene (HIPS). GPPS has less dimensional stability and is brittle compared to HIPS. In most cases, it is combined with butadiene to reinforce its properties.
Thermoplastic Elastomer (TPE)
Thermoplastic elastomer (TPE) or thermoplastic rubber is a combination of plastic and rubber materials. As such, it behaves and performs like rubber but is processed like plastic. Most product designers and engineers prefer this material because of its elasticity.
TPE is recyclable and the recycled materials can be combined to create TPEs. Most common products from this material are footwear, auto parts, medical devices, and pet products.
Thermoplastic Polyurethane (TPU)
Thermoplastic polyurethane (TPU) is a thermoplastic elastomer that is also commonly used in injection molding. It has a rubber-like elasticity and can be used as a replacement for hard rubber.
TPU is often chosen over TPE when the part will be exposed to chemicals and high temperatures.
Other Materials for Plastic Injection
The materials listed above are not the only materials for plastic injection molding. Depending on the requirements, you can combine the properties of two different polymers to meet them. Some of the various bends include:
- PC/ABS – a combination of polycarbonate and acrylonitrile butadiene.
- PC/PBT – a combination of PC plastic and polybutylene terephthalate (PBT), commonly used on electrical and electronics.
- PPE/PS – a combination of polyphenylene (PPE) and polystyrene (PS), which is used in environmental engineering, fluid engineering, and potable water applications.
Conclusion
The list of materials for plastic injection molding is long and often confusing. That means you need to consult an expert to choose them for your next plastic injection molding project.