7 Additive Manufacturing Technologies & The Materials
Additive Manufacturing (AM) or most commonly known as 3D printing is defined as a process of joining materials layer by layer to form a part from 3D CAD model as opposed to subtractive and formative manufacturing methodologies. Additive Manufacturing (AM) is the official industry standard term but the 3D printing has become the de facto standard term and is the most widely used terminology.
Nowadays, AM becomes a trend in the market and has a broad implication across various industries. Many of the AM system manufacturers have created unique process and material names to differentiate themselves from their competitors. In fact, many of these different systems employ the similar AM technologies and materials. Fortunately, AM industry has an industry standard system for grouping AM processes and materials.
Additive manufacturing processes are generally grouped into 7 technologies with their standard approved terminology according to ISO/ASTM 52900 standard:
- (I) VAT Photo-Polymerization
- (II) Materials Extrusion
- (III) Materials Jetting
- (IV) Powder Bed Fusion
- (V) Binder Jetting
- (VI) Direct Energy Deposition
- (VII) Sheet Lamination
1. VAT Photo-Polymerization
Definition:
An additive manufacturing process in which liquid photopolymer in a vat is selectively cured by light-activated polymerization.
Common used Techniques:
Stereo-lithography (SLA)
SLA is the first patented and commercialized AM process. Top surface of a VAT of liquid photopolymer resin is cured by UV laser to solidify the pattern layer-by-layer to create a solid 3D model from bottom to top.
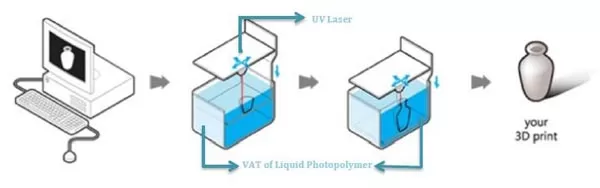
Courtesy of Materialise
Digital Light Processing (DLP)
Unlike the SLA’s methodology that scans the top surface of the liquid photopolymer in a vat, DLP polymerization systems project light from below the vat and cure the photosensitive resin through the optical window. This method requires less amount of photosensitive resin in the vat compared to SLA.
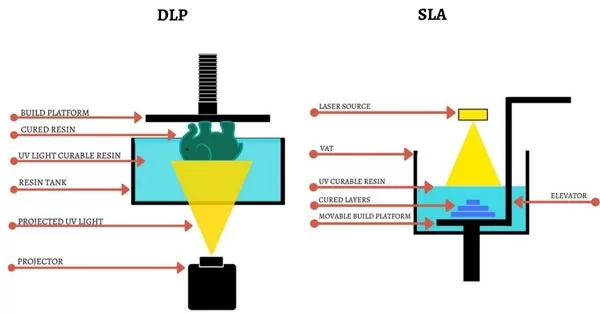
A diagrammatic representation of the working of DLP vs SLA. – Courtesy of Materialise
Common Materials:
- Polymers: UV-curable Photopolymer resin
- Composite
- Ceramics
2. Materials Extrusion
Definition:
An additive manufacturing process in which the material is selectively dispensed through a nozzle.
Common used Technique:
Fused Deposition Modeling (FDM)
Fused Deposition Modeling is the most common material extrusion process and is trademarked by Stratasys. Material is extruded through a nozzle, heated and then deposited layer by layer. The printer has more than one printing nozzle. One nozzle will be used for build material while the other for supports material.
Common Materials:
- i. Polymers (e.g. ABS, PC, Nylon, PC+ABS, ULTEM, PLA)
- ii. Composite (e.g. Clay filled polymer, Metal filled polymer, Wood filled polymer)
- iii. Ceramics
- iv. Concrete
- v. Food (e.g. Chocolate)
- vi. Living cells
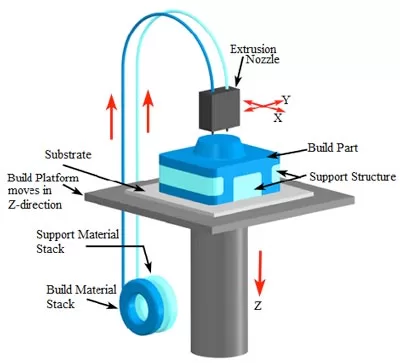
A Schematic diagram of FDM Process. – Courtesy of Researchgate.net
3. Materials Jetting
Definition:
An additive manufacturing process in which the build material droplets are selectively deposited in the build platform. The materials used in material jetting are typically photopolymers or wax-like materials that can be used as investment casting patterns.
Common used Technique:
PolyJet
The name PolyJet is now used for printers from Stratasys. It often uses multi-nozzle print heads to print different materials simultaneously. The materials are photopolymers and are cured by UV light as they are deposited.
Stratasys system uses dissolvable support material, which is usually made of polyethylene, propylene and glycerin. Once finish printing, the PolyJet parts are removed from the build platform and exposed to pressurized water. The supports can be removed as much as possible without dissolving it. Afterwards, the parts will then immersed in a chemical solution to dissolve the rest of the supports.
Common Materials:
- i. Polymers (e.g. ABS, PC, PS, PP, HDPE, PMMA)
- ii. Wax-like materials
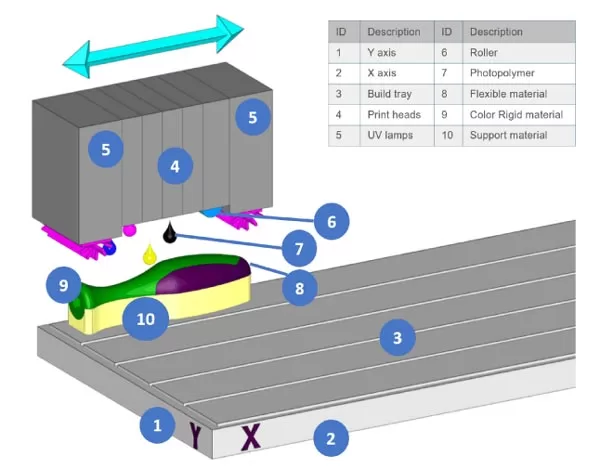
Schematic Diagram of PolyJet Process by Stratasys – Courtesy of Stratasys
4. Powder Bed Fusion
Definition:
An additive manufacturing process in which the thermal energy selectively fuses the region of a powder bed. Both polymers and metals are available for powder bed fusion process.
Common used Technique:
Selective Laser Sintering (SLS)
This process is mainly applied for polymers. In SLS, the laser scans across the region of polymer powder bed, then the platform moves down a layer and another fresh layer of powder will spread over the previous layer. The unfused powder surrounding the part is compacted enough to serve as supports and hence no additional supports are needed.
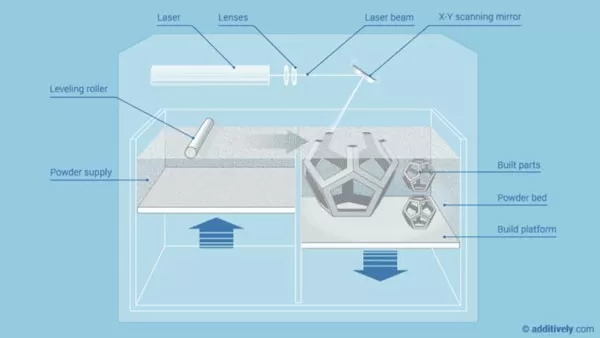
Schematic Diagram of SLS
Selective Laser Melting (SLM)
The process mechanism is identical to SLS but using higher laser power and supports are needed in order to anchor the parts from the build plate. This is necessary especially when melting the high melting point of metal powder. There is very high risk of part distortion caused by high thermal gradient during the process, hence the supports are very vital in this process to prevent the parts from warping and also for heat dissipation.
Electron Beam Melting (EBM)
EBM is another metal powder bed fusion process that is identical to SLM. However, it uses electron beam instead of laser. The EBM surface finish is coarser than SLM. However, the EBM process is faster and produces less residual stress in parts in comparison to SLM.
Common Materials:
- i. Polymers: Nylon (by SLS process)
- ii. Metals: Titanium, Stainless Steel, Cobalt Chrome, Aluminum, Tool Steel, Copper (by SLM and EBM process)
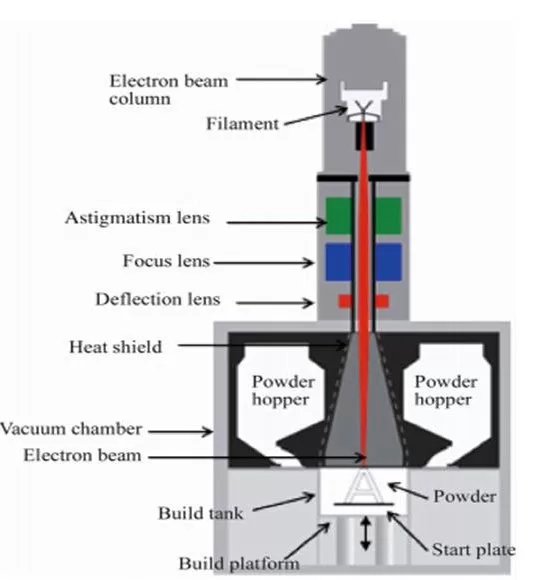
Schematic Diagram of EBM
5. Binder Jetting
Definition:
An additive manufacturing process in which the liquid bonding agent is selectively deposited to join the powder in a powder bed system. This process can be used in a wide range of materials such as polymers, metals and ceramics. The metal parts produced by Binder Jetting require going through secondary process called sintering and infiltration in order to get a higher density of the part. This process capable of building parts at relatively high speed, however, for metal parts, the additional time for sintering and infiltration slower down the overall process.
Common Materials:
- i. Polymers: ABS, PA. PC
- ii. Metals: Stainless Steel
- iii. Ceramics: Glass
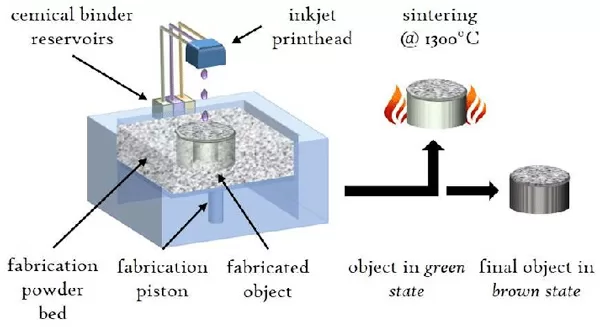
Schematic Diagram of Binder Jetting – Courtesy of Researchgate
6. Direct Energy Deposition
Definition:
An additive manufacturing process in which the focused thermal energy is directed from a nozzle to fuse the materials by melting immediately as its deposition on the target. The thermal energy can be in laser or electron beam. The material can be metal powder or wire.
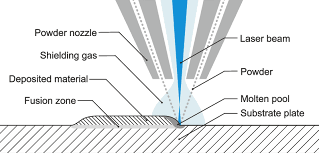
Schematic Diagram of Metal Powder Direct Energy Deposition – Courtesy of Researchgate.net
This process is commonly used for production of large parts. It also widely used for repairing worn or broken parts or to add features to an existing part.
Common Materials:
- i. Metals: Titanium, Cobalt Chrome, Inconel, Stainless Steel
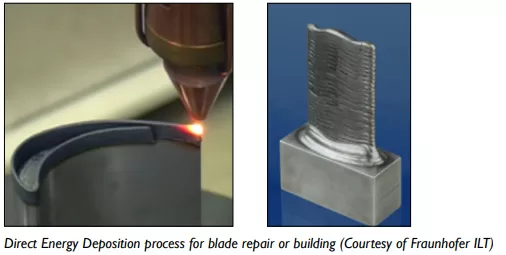
Schematic Diagram of Direct Energy Deposition for blade repair
7. Sheet Lamination
Definition:
An additive manufacturing process in which sheet of materials are bonded to form a part.
Common used Technique:
Laminated Object Manufacturing (LOM)
LOM was the first Sheet Lamination technique developed by Helisys. The paper is coated with polymer which is served as an adhesive. A heated roller is used to laminate the successive layers of sheets. The laser beam is used to cut the 2D profile of the part at each layer.
Ultrasonic Additive Manufacturing (UAM)
Ultrasonic Additive Manufacturing (UAM) was another Sheet Lamination technique developed by Fabrisonic. It uses ultrasonic welding to bond the thin layers of metal foils. The layers are welded together by combination of ultrasonic and compressive force created by the system’s rolling sonotrobe. Once the layers are bonded, the metal is milled to cross sectional shape defined by CAD data. The process continues until it finishes the part.
Common Materials:
- i. Metals
- ii. Polymers
- iii. Paper
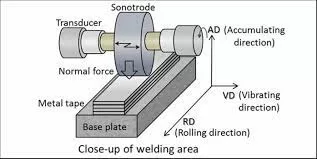
Schematic Diagram of Ultrasonic Additive Manufacturing – Courtesy of insidemetaladditivemanufacturing.com