As smart factories revolutionize manufacturing, plastic injection molding emerges as a crucial technology, enhancing efficiency and precision in production processes. Integrating automation and real-time data analytics allows you to produce complex plastic components with remarkable speed and consistency.
In an innovative factory environment, the ability to adapt rapidly to changing demands is vital, and plastic injection molding supports this agility. With advanced machinery and optimized workflows, you can streamline operations and reduce waste, driving down costs while improving product quality.
The synergy between plastic injection molding and smart factory principles boosts productivity and enables more significant innovation in product design. As you explore this topic, you’ll discover how these advancements can transform your manufacturing capabilities and position your business at the forefront of your industry.
Fundamentals of Plastic Injection Molding
Understanding the essential aspects of plastic injection molding is crucial for optimizing production processes. Key components include the injection molding process, materials used, machinery specifications, and design considerations necessary for effective implementation.
Overview of Injection Molding Process
The injection molding process involves several stages. Initially, raw plastic material is heated until it becomes molten. The molten plastic is then injected into a mold under high pressure. Once it cools, the mold opens, and the finished part is ejected.
This process is efficient for producing large quantities of complex shapes. It allows for precise control over dimensions and details. Cycle times can vary based on the size and complexity of parts but typically range from seconds to minutes.
Materials and Machinery
The selection of materials in plastic injection molding is diverse. Common materials include thermoplastics like ABS, polycarbonate, and nylon. Each material has unique properties affecting durability, flexibility, and appearance.
The machinery used in this process consists of an injection molding machine, which typically includes three components: the injection unit, the clamping unit, and the mold. The machine type and configuration depend on the application and desired output. Matching the machine specifications with the material properties for optimal results is essential.
Design Considerations for Injection Molding
Designing for injection molding requires attention to various factors. Part geometry is critical; complex features may necessitate advanced mold designs. Consider wall thickness, as uniformity helps prevent defects.
Incorporating draft angles in the design eases mold release. Gate locations, which affect filling patterns and overall part quality, should also be considered. Tolerances should also align with manufacturing capabilities. Proper design can reduce costs and improve cycle times, enhancing production efficiency.
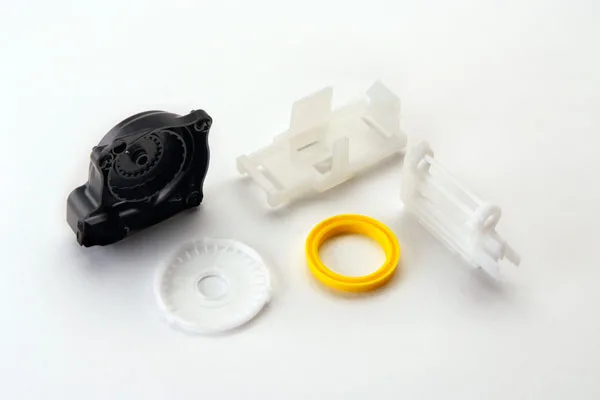
Precision plastic parts
Integration of Smart Factory Principles
Integrating smart factory principles within plastic injection molding enhances efficiency, reduces waste, and improves quality. Key technologies like IoT and data analytics are crucial in optimizing these processes, leading to more reliable production outcomes.
Application of IoT in Injection Molding
The Internet of Things (IoT) transforms plastic injection molding by enabling real-time monitoring and control of machinery. Sensors placed on injection molding machines collect temperature, pressure, and cycle times data.
This data is transmitted to centralized systems, allowing operators to adjust immediately. For instance, if a temperature deviation is detected, adjustments can be made automatically to prevent defects.
Advantages of IoT in injection molding:
- Real-time insights: Monitor machine performance continuously.
- Enhanced decision-making: Data-driven adjustments improve processes.
- Reduced downtime: Quickly address issues before they escalate.
Data Analytics and Process Optimization
Data analytics enables manufacturers to significantly optimize their injection molding processes. By analyzing historical data, you can identify trends and areas for improvement.
Key performance indicators (KPIs) such as cycle time and defect rates can be tracked and analyzed. This leads to actionable insights that inform process adjustments.
Key benefits include:
- Process efficiency: Identify bottlenecks and streamline operations.
- Improved quality: Target specific defects for corrective measures.
- Cost savings: Reduce waste and material costs through better processes.
Predictive Maintenance and Quality Control
Predictive maintenance uses data to anticipate machine failures before they happen. This is particularly important in plastic injection molding, where downtime can be costly.
Sensors predict when a machine component will likely fail, prompting you to perform maintenance proactively. This approach prevents unscheduled shutdowns and maintains production quality.
Benefits of predictive maintenance:
- Minimized downtime: Address issues before they affect production.
- Lower maintenance costs: Targeted interventions reduce expenses.
- Consistent quality: Maintain steady production standards.
If you need help integrating smart factory principles into your plastic injection molding processes, consider contacting Nicerapid.com for a quote tailored to your project.